We continue into the second part of an entertaining set of articles from ILUMINAR, focused on the “brief” history of artificial grow lighting.
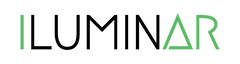
The following is an article produced by a contributing author. Growers Network does not endorse nor evaluate the claims of our contributors, nor do they influence our editorial process. We thank our contributors for their time and effort so we can continue our exclusive Growers Spotlight service.
Disclaimer
This article was originally published on the Iluminar blog. If you would like to read the original article, please click here.
It might have occurred to you that this brief history of grow lighting isn’t actually all that brief, as we’re now into our second post and haven’t even got to High Pressure Sodium (HPS) lamps yet. It even shocked us when we started doing the research, but believe it when we say that this is, in fact, an extremely brief history. We’re skirting around a lot of references and it could be argued that we abridged too far (pun intended); in reality we bit off more than we could chew. There are an awful lot of clever ideas that went into modern lighting technology and it’s nearly impossible to cram it all into a single blog.
Still, there’s no harm in trying – so here we go again.
Whitesnake knows what we’re doing. Here we go again.
In part one we left you somewhere between Geissler tubes in 1857 and the birth of the fluorescent light in the 1920’s. At this point, it would be wise to avoid confusing you further with our trip down gas “glow” discharge technology and side-step into the world of the gas vapor discharge lighting. The reason we are ditching fluorescent lighting is that in reality its low intensity limits it to close-proximity crops that are a tiny fraction of the the horticultural lighting industry. Perhaps we’ll look at them in detail in a later post, but there are bigger historical fish for us to fry.
Enter the low pressure mercury vapor lamp. Although mercury lamps using electrical arcs can trace their lineage back to 1835 for the first observed mercury arc itself, and 1860 for the first mercury vapor light, the first commercial success was in 1901 at the hands of Peter Cooper Hewitt, whose low pressure mercury vapor lamps were used in many industrial applications including street lighting. However, this design was very crude and required a lot of mercury. By the 1930’s, improvements from OSRAM-GEC and General Electric had turned the mercury vapor lamp into a far more viable luminaire for general use.
At the same time that mercury vapor lamps were being improved, a gentleman named Arthur H. Compton, a future Nobel winner, invented the first low-pressure sodium (LPS) bulb. It didn’t work very well, because the alkali metal sodium kept destroying the electrodes and eroding the glass, but it showed serious possibilities. Sodium lamps are desirable due to their extremely high efficiency when converting electrical energy into usable light. The only catch is that high efficiency results in light which is almost entirely yellow and is therefore limited in its application.
Regardless, in 1932 a tiny Dutch company called Phillips launched the first commercially viable LPS lamp. Just four years later, in 1936, the same tiny Dutch company launched the first commercial high-pressure mercury vapor lamp. The new high-pressure lamp was based upon breakthrough research from German researchers Kuch and Retschinsky, who in 1906 developed the fused quartz arc tube. Using quartz instead of typical glass allows mercury to vaporize at much higher pressures, thereby boosting efficiency. Are you starting to see where the high-pressure sodium (HPS) comes from yet?
Haha, fooled you, because that’s not how we actually got to HPS lamps.
Why? For the same reason that Arthur H. Compton’s original LPS lamp failed: Sodium is a very aggressive metal alkali, and when it’s vaporized, it simply eats its way through most glass, silica or quartz-based materials. You can’t sustain a sodium lamp reaction in a fused quartz arc tube because it just doesn’t work for long enough to be viable.
The next stage in our story is prompted not by the invention of a lamp, but by the invention of a new material with a rather funky name: Lucalox. Lucalox was the invention of Robert L. Coble of General Electric and was the GE brand name for a material that we know today as aluminum oxide ceramic, an extremely heat-resistant and strong material that can withstand the highly caustic nature of sodium vapor at the pressures necessary to improve both the color rendering index (CRI) and the lifespan of the bulb.
However, it would still be another nine years until yet another GE team would present the world with it’s first high pressure sodium bulbs in 1964. This team was made of William Louden, Kurt Schmidt and Elmer Homonnay. With further developments and improvements made in the 1980’s, HPS rapidly became the most common street lamp in the world, and the workhorse of supplemental lighting in greenhouses around the world. But there was still much more improvement to come.
Throughout the history of the lighting industry, supplemental agricultural lighting has always borrowed technology that was been developed for people and not plants. Thus the adage, “Lumens are for Humans.” Well in this case it’s literally true.
However as world populations continued to grow over the 20th century, a new need for artificial lighting began to take shape: lighting specifically designed for plants. In the latter half of the century things began to change…
Thanks for reading!
The ILUMINAR team
10 Best Gift Ideas for Cannabis Connoisseurs and Growing Aficionados (2022)
December 7, 2022Developing and Optimizing a Cannabis Cultivation System
December 14, 2021Dealing with Insomnia: How Can CBD Help?
December 10, 2020Your Guide to Sleep and CBD
December 7, 2020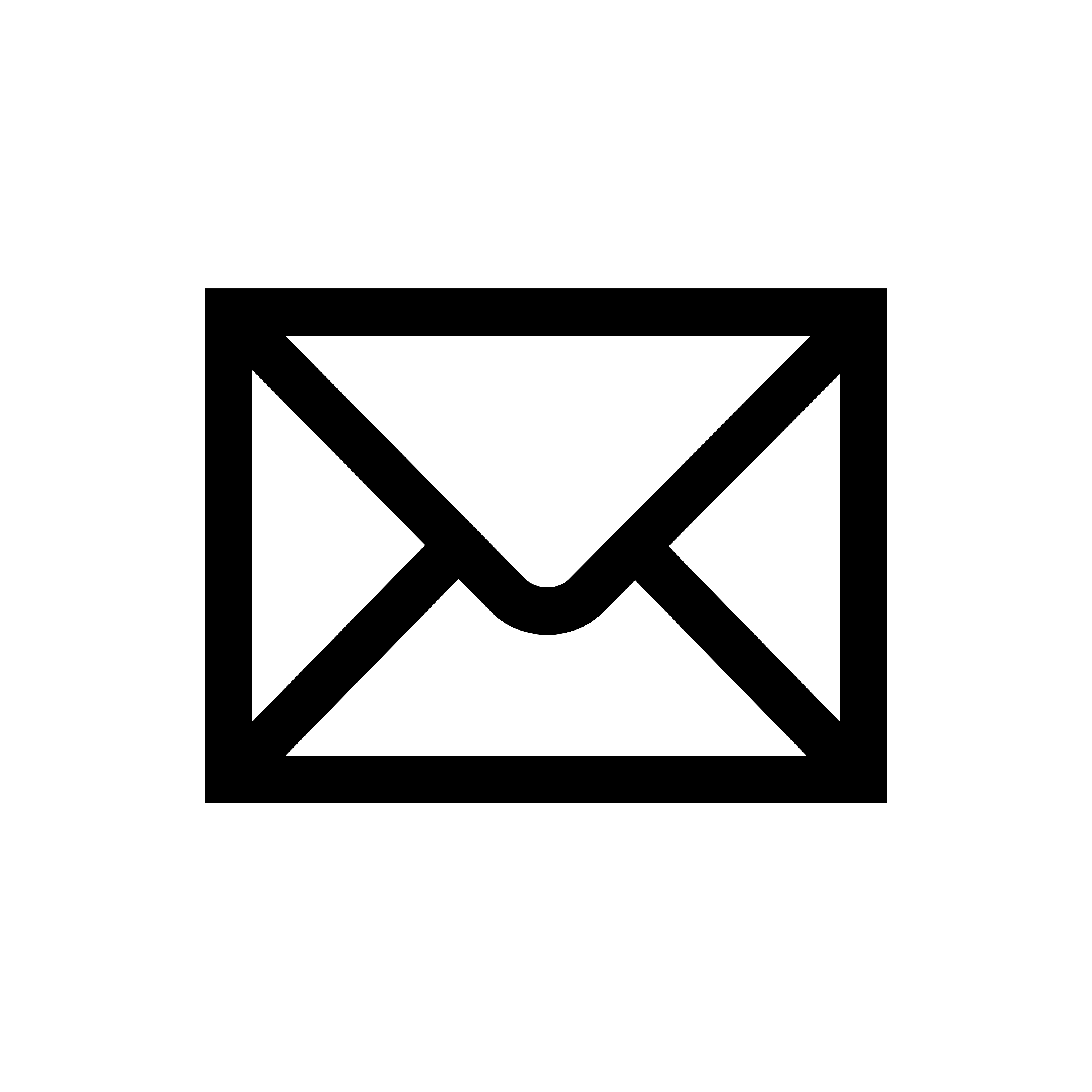
Do you want to receive the next Grower's Spotlight as soon as it's available? Sign up below!
Resources:
Want to get in touch with Iluminar? They can be reached via the following methods:
- Website: https://www.iluminarlighting.com/
- Email: sales@iluminarlighting.com
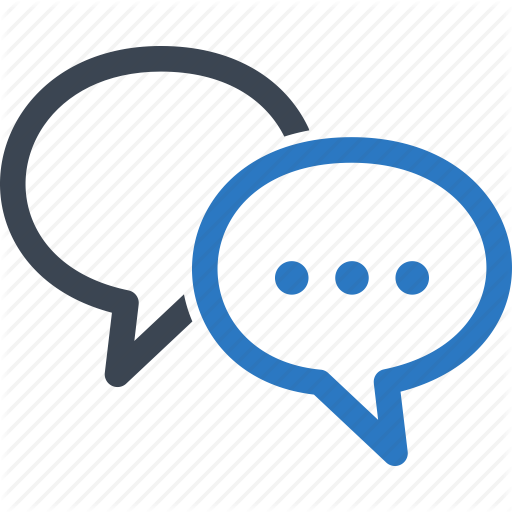
Do you have any questions or comments?
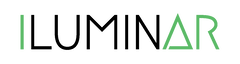
About the Author
Iluminar is a veteran lighting brand with growers behind the wheel. We have spent our years under lights as well. We have been in the industry for over 20 years and proud of it.