In this Growers Spotlight, we interview Shane Hutto. Shane has Bachelor's and Master's Degree in Horticulture with a focus on extraction from Oklahoma State University. Shane is also the owner of Horticultural Solutions Ltd and Horticultural Extracts LLC.
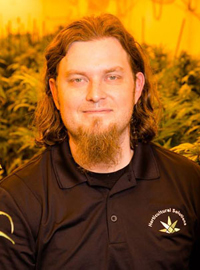
He has worked in one of the largest single-site greenhouses in the United States, the Metrolina Greenhouses. Shane has also worked in extractions for many years for Oklahoma State University, and currently consults for commercial cannabis grow operations on greenhouse designs.
In this Growers Spotlight, we discuss terminology, equipment, brands, and what options a grower should look at when purchasing a greenhouse.
The following was an interview with an industry expert. Growers Network does not endorse nor evaluate the claims of our interviewees, nor do they influence our editorial process. We thank our interviewees for their time and effort so we can continue our exclusive Growers Spotlight service.
To skip to any section within this article, click the links below:
Want to listen to the article? Check out our podcast.
The Science of a Greenhouse
A greenhouse is any building or structure that is designed to capture the heat and light from the sun for the purposes of growing plants. Greenhouses allow for more precise control of the environment in which plants grow.
What You Should Know About Greenhouses
Greenhouses are very sophisticated machines and how well they run depends on how well they’re designed and built. Shane Hutto
The Greenhouse Market
Nobody wants to invest a million dollars in a greenhouse and 5 years later see it rusted to hell.Shane Hutto
The Technology of Modern Greenhouses

10 Best Gift Ideas for Cannabis Connoisseurs and Growing Aficionados (2022)
December 7, 2022Developing and Optimizing a Cannabis Cultivation System
December 14, 2021Dealing with Insomnia: How Can CBD Help?
December 10, 2020Your Guide to Sleep and CBD
December 7, 2020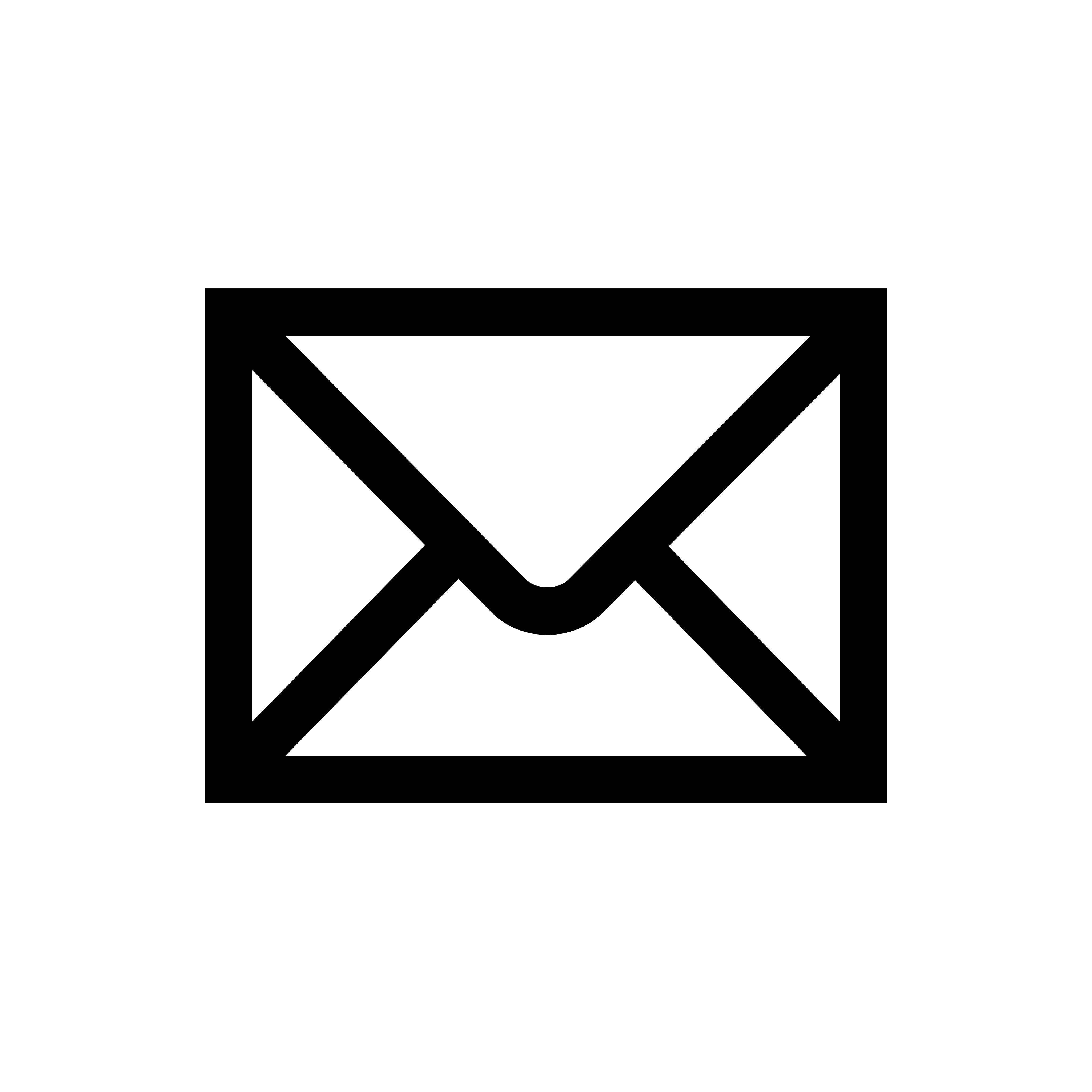
Do you want to receive the next Grower's Spotlight as soon as it's available? Sign up below!
Want a consultation from Shane for a grow operation?
The best way to find Shane is through his website hort-solutions.com. There’s a contact form on the website. You can find the office phone number on there. Shane's secretary can set up an appointment. You can also email sales@hort-solutions.com and somebody will take care of you.
Resources:
- Horticultural Solutions -- Consult with Shane Hutto on your own greenhouse.
- Priva -- Horticultural Automation
- Delta-T Solutions -- Environmental Control Systems
- Dosatron -- Automated Irrigation Systems
- DryGair -- Commercial Dehumidification Systems for Greenhouses
- GGS-Greenhouses -- High-Quality Greenhouses
- Want to see a major greenhouse in production? Check out Episode 1 of Canna Cribs.
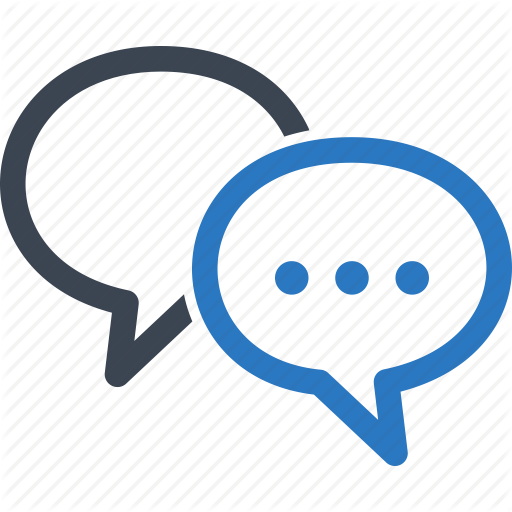
Do you have any questions or comments?
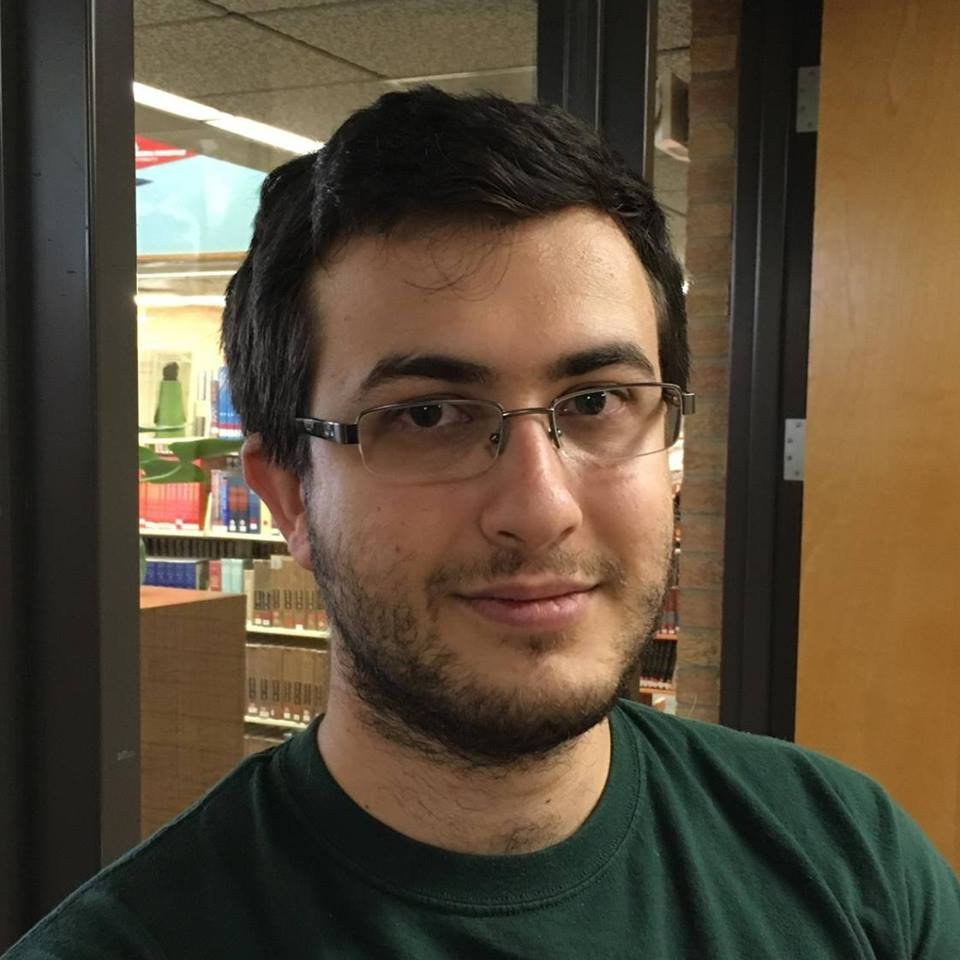
About the Author
Hunter Wilson is a community builder with Growers Network. He graduated from the University of Arizona in 2011 with a Masters in Teaching and in 2007 with a Bachelors in Biology.