Evio Labs tells us why careful planning and process control are essential to ensure consistent high-quality products for your consumers.
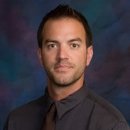
The following is an article produced by a contributing author. Growers Network does not endorse nor evaluate the claims of our contributors, nor do they influence our editorial process. We thank our contributors for their time and effort so we can continue our exclusive Growers Spotlight service.
The Cannabis industry is booming right now. In many markets, competition is stiff and the urgency to create new products is high. In Colorado alone there are 255 Medical Infused Product Manufacturers and 273 Retail Product Manufacturers1 (sometimes called extractors or processors). Across the United States, the number of similar companies is 10 times higher. How do you rise above the competition? How do you differentiate your products? The answer: create a product that sells itself.
The market clearly wants clean and safe products. As regulators enforce an increasing number of public health regulations, the number of pesticide recalls and health concerns will only continue to grow. Companies that wish to survive this period of dynamic expansion and contraction will need to build a client base that both trusts and loves their products.
How is this done? Process Control.
Process Control
Process Control is an engineering discipline concerning the mechanisms, algorithms, procedural steps, and equipment for maintaining the output of a specific process within a desired range2. Any process must be defined, as should all the equipment, equipment settings, documentation, and steps needed to create the product (specifically, Cannabis concentrates).
This process must also be monitored. Monitoring should include testing at various points of product development. Monitoring helps detect an out-of-control situation. Once an out-of-control situation is detected, personnel can bring the process back into control by following predetermined protocols (or SOPs).
Editor’s Note: An “out-of-control” situation does not necessarily mean the process has gone off the rails. It just means it’s outside of the normal, desired situation.
The purpose of process control is to ensure a process is predictable and operates at its highest efficiency within normal variability, which is extremely useful to both employees and managers. It is also used to quickly identify and resolve process problems, in addition to identifying situations where the process could be improved. Thorough process control should increase product throughput and yield, decrease energy consumption, decrease off-specification (or non-compliant) product, increase safety, extend equipment lifetimes, and decrease labor costs. Compliance with process control is a major part of current Good Manufacturing Practices (cGMP), and when Cannabis becomes federally regulated, those companies following cGMP as well as 21 CFR 210 and 21 CFR 211 will have a significant head start over those who are not2.
Using Process Control
Now that we understand what process control is, how do we use it? In this article, we will demonstrate where and how to use process control when producing Cannabis concentrates from trim using carbon dioxide (CO2) extraction techniques.
Our first step is to identify an ideal product. What do we want to sell? What is the best product we can manufacture? The answers to these questions will drive every other decision the business makes and dictate the capital expenses that follow. For example, if we want to make an ideal wax or shatter, the extraction equipment and methods will differ. Once the equipment is purchased, we’ll need to optimize our operation procedures for the equipment.
The second step in product development is to create a documented production plan. Which products will be made? How do we define an “acceptable product?” If we make a CO2 extract and distill it, is a product with 65% THC our goal? Probably not. Do we only want to sell distillates above 80% THC? What are the terpene concentrations? Do we even include terpenes? These decisions will form any ideal process. Then we can design systems to achieve our goals and begin to define the production process.
Next, we’ll need to test any raw materials! Always do this. What comes out of a process will always depend on what goes in, no matter how talented your personnel are. Remember, when creating extracts, we are concentrating everything that is in the sample, not just the cannabinoids. Were there pesticides in the incoming trim? Heavy metals? What is the chemotype (cannabinoid and terpene concentrations)? Each of these compounds is important because we know that the effects of these compounds are synergistic3. Knowing these starting points will enable us to reliably predict what products will exit the extraction process. It will also allow us to reject poor quality starting materials that don’t meet our internal specifications.
What comes out of a process will always depend on what goes in
This thought naturally leads us into establishing acceptability criteria. Every processing step affects our products; therefore, we need to establish acceptability criteria for each step. Though some variation from batch to batch is normal, acceptability criteria can help us measure what is beyond normal variability and investigate what made a batch fail.
Typically, this is accomplished with control charts in the pharmaceutical industry (and many other industries). Plots showing normal batch endpoints (concentrations, temperatures, pressures) are plotted against upper and lower limits of variability. See Figure 1. When a batch exceeds either of these limits, investigations are performed to answer why. Did a power outage affect the temperature gradient? Was a SOP not followed directly? Control charting makes it easy to define when things go wrong as well as correct the error. The best part of using control charts is that regulators will be overwhelmed with your compliance, and you’ll easily pass any audit you’ll ever have. Additionally, if your trim passes all contaminant tests and has cannabinoid and terpene concentrations that meet your specifications, it can be sold and used for extractions by others.
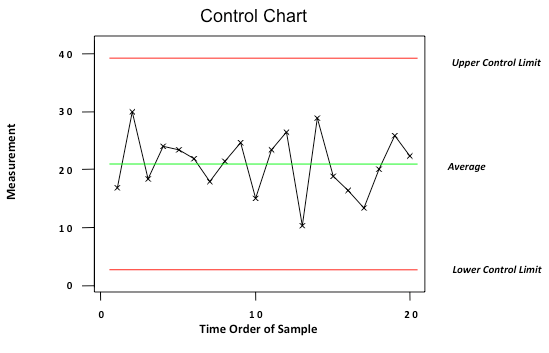
The tobacco industry has been doing this for decades. How do they make millions of cigarettes all appear and taste the same? The answer is process control during the blending of tobacco batches to meet strict acceptability criteria on chemotype and additive concentrations4. Process control means controlling raw materials and every processing step , and never deviating from this process. Data from each step compared to predefined acceptance criteria is critical to achieving process control. If we don’t test, we don’t know.
Tunable Processes
The next step in our ongoing example is the extraction of the trim materials. Carbon dioxide extractions are sometimes thought of as “tunable processes”. This is because it is possible to manipulate the temperature and pressure of the supercritical CO2 to create the desired products. It also means we’ll need high levels of control to ensure that each processor is achieving the same temperature and pressure gradients for the same time points. Only high-quality training and strong Standard Operating Procedures (SOPs) can guarantee process control and high-quality products. Without process control, we’ll waste time and money wondering why the products are changing batch to batch. This tunable nature gives us opportunities for in-process testing, allowing us to test at different temperatures and pressures to obtain data on how to optimize our initial SOPs. Then we can perform these in-process tests to maintain acceptability criteria for normal batch production. These same principles apply to any extraction technique or technology.
The next step in our product development example is distillation. In distillation, components in a complex mixture are separated by heating them to their specific boiling points and then condensing them in a collection vessel. Highly controlled distillation will result in high purity distillates that are free of contaminants. Good SOPs control the temperature and pressure gradients, as well as the time of the runs, to exact seconds and degrees. Temperature and pressure changes will definitely change the end product.
It should be known what happens if the temperature deviates too much during your distillation. That way, when tracking our control charts, we know what happened when we see lower quality products. At PhylaTech, we see many distillation products that should have hypothetically reached over 80% purity, but the process set points (temperature and pressure) were not controlled, leading to side reactions of THC. The distillation mixture can also affect the concentrate’s final viscosity, which is important if making vape cartridges. The viscosity also affects the stability and shelf-life of products.
Final Products
Now that we’ve established a highly controlled process to produce the best products on the market, do we want to think about drug delivery? All kinds of technologies exist for optimizing product solubility and bioavailability. Examples include spray drying, coating beads, using amorphous solids, achieving size reductions via hot melt extrusion (microparticles and nanoparticles), using lipid formulations, and encapsulating in capsugel. These types of advanced higher-order processes are the topic of future articles, but are important to keep in mind for future business goals.
Product quality depends on you. If you do the homework, do the testing, and control the processes, your products will sell themselves. Remember, a good laboratory isn’t there to just pass or fail products, but will support process development and process control efforts with reliable data and in-depth understanding of any processes.
References
- https://www.colorado.gov/pacific/enforcement/med-application-and-licensing
- https://www.fda.gov
- Russo EB. Taming THC: potential cannabis synergy and phytocannabinoid-terpenoid entourage effects. British Journal of Pharmacology. 2011;163(7):1344-1364. doi:10.1111/j.1476-5381.2011.01238.x.
- https://cannabisdigest.ca/augmented-cannabis-oil/
- http://hemphacker.com/why-winterization-stabilizes-hash-oil-extracts/
- Carbonyl Compounds Produced by Vaporizing Cannabis Oil Thinning Agents. Troutt, William D. et al.
10 Best Gift Ideas for Cannabis Connoisseurs and Growing Aficionados (2022)
December 7, 2022Developing and Optimizing a Cannabis Cultivation System
December 14, 2021Dealing with Insomnia: How Can CBD Help?
December 10, 2020Your Guide to Sleep and CBD
December 7, 2020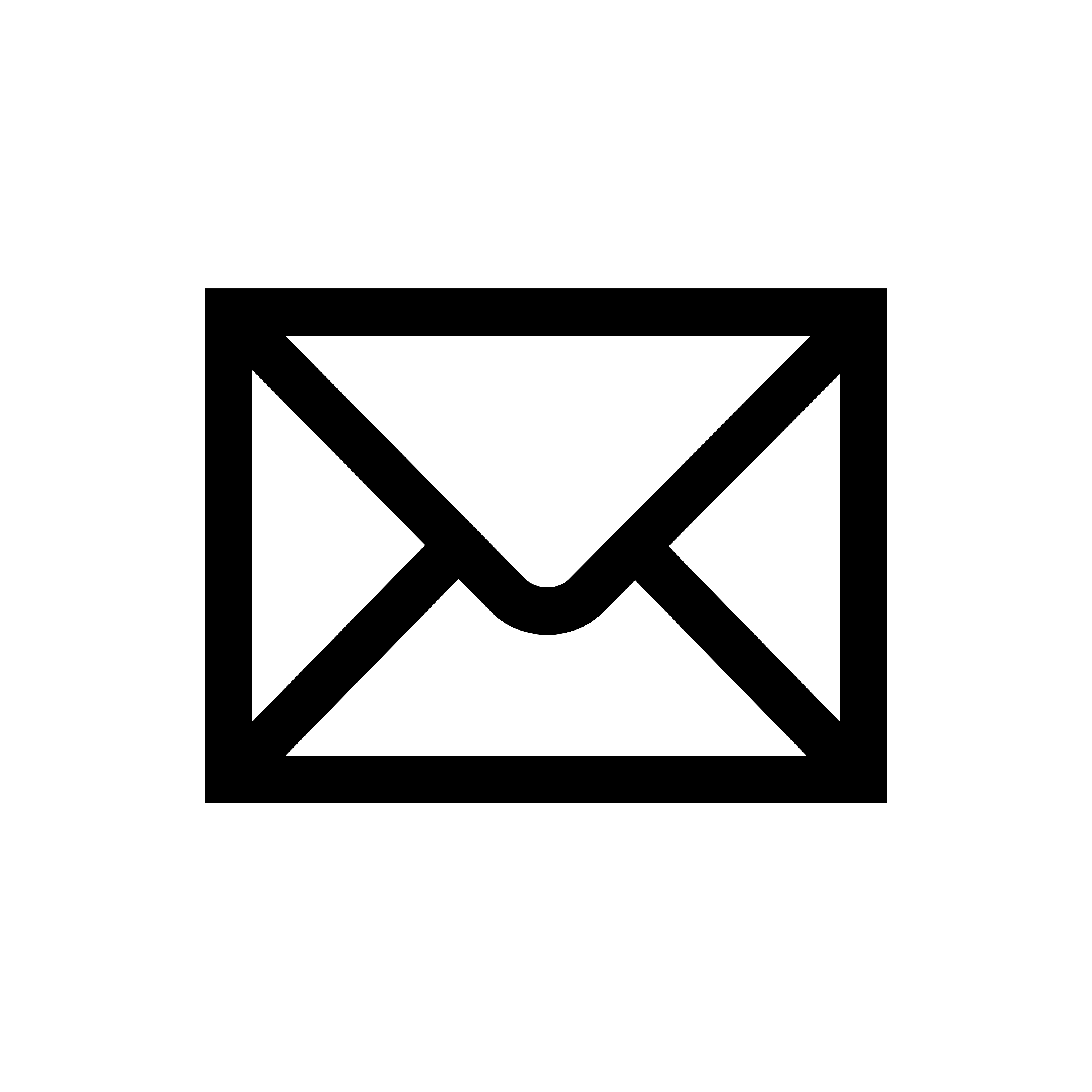
Do you want to receive the next Grower's Spotlight as soon as it's available? Sign up below!
Resources:
Want to get in touch with Evio Labs? They can be reached via the following methods:
- Website: http://eviolabs.com/
- Email: info@eviolabs.com
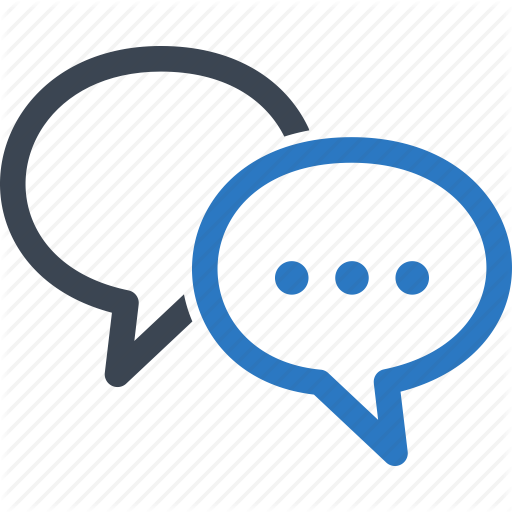
Do you have any questions or comments?
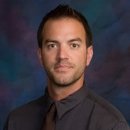
About the Author
Stephen Goldman is an analytical chemist with extensive industrial and academic laboratory experience. He came to EVIO from PhytaTechSM and has expertise in GC, HPLC and mass spectrometry, chemical and biochemical engineering as well as project and business management. Prior to joining PhytaTech, Stephen served as an analytical chemist at the CLIA and CAP certified Forensic Laboratories, overseeing toxicology testing. Stephen has published a number of research papers in the fields of biological and analytical chemistry. He is a member of the American Institute of Chemical Engineers, American Association of Pharmaceutical Scientists and the American Chemical Society. Stephen has a Master of Science in Pharmaceutical Chemistry with Honors from the University of Kansas and a Bachelor of Science in Chemical and Biochemical Engineering from the University of Iowa.