In this contributor article, Brandy Keen of Surna talks about the amazing benefits of using a test room in commercial cannabis facilities.
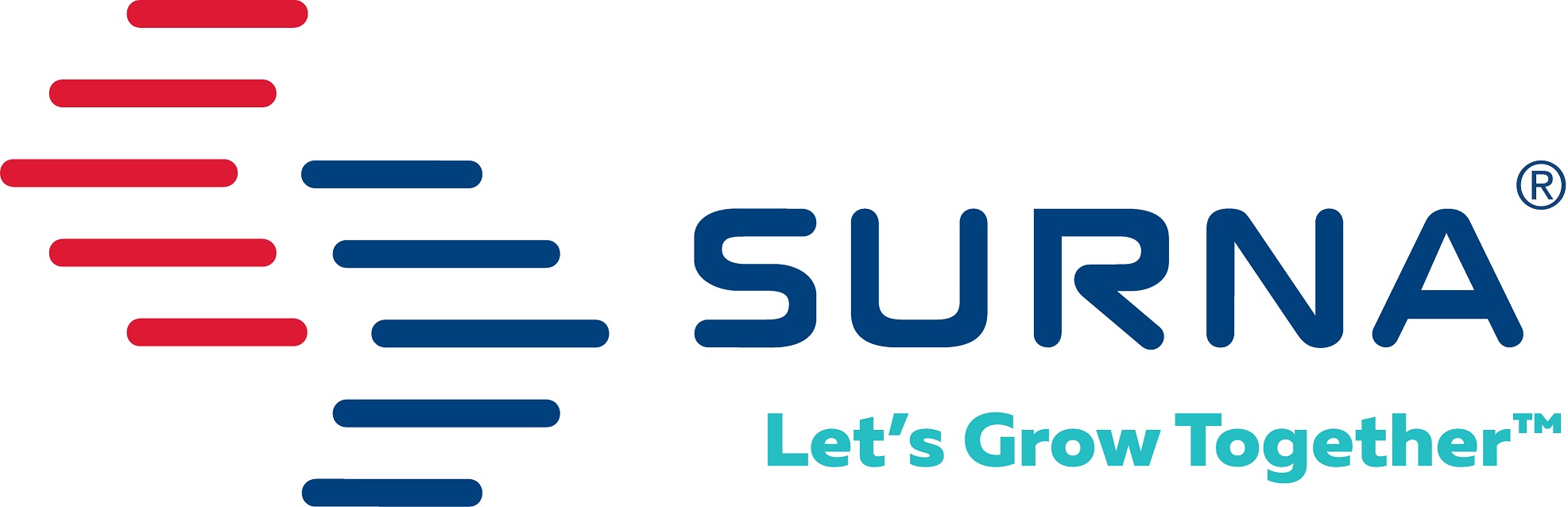
The following is an article produced by a contributing author. Growers Network does not endorse nor evaluate the claims of our contributors, nor do they influence our editorial process. We thank our contributors for their time and effort so we can continue our exclusive Growers Spotlight service.
Commercial cultivators are continually honing their craft so that every harvest produces only the best crop. However, staying at the top of the market means improving all the time. Without continued refinement, whatever competitive advantages growers may have seen will quickly disappear as a once novel formula becomes just part of the day-to-day at a facility. If growers want to stay at the top, they can’t become complacent. They need to keep the improvements coming.
Staying competitive in a growing market mean growers may have to get out of their comfort zone, and since refinement is the result of trying something new, growers need to be willing to leave their comfort zone when it comes to their grow strategies. To stay ahead of the curve, commercial growers need to be open to experimenting with new products, technologies, methods, amendments, Standard Operating Procedures (SOPs), and of course, their own new innovations. By evaluating strategies and products under controlled conditions, growers can dial-in what works best for their facility and continue improving quality. The most streamlined way to achieve this kind of control is with a test room.
Test rooms are a great place for growers to not only hone their craft through experimentation, but such a space will also allow them to stay on top of the latest industry practices they want to use to increase profits - either an improved product or simply by using the data to drive costs down. For this reason, test rooms are a must-have for any facility that wants to remain competitive in the booming cannabis market. Therefore, investing in a 10-20 plant test room in a facility is one of the best investments a grower can make in their operation.
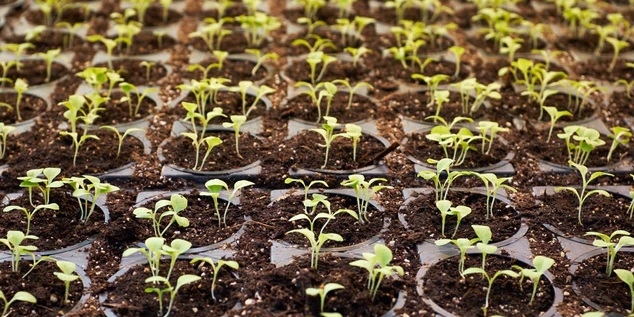
A test room is not meant to replace or compete with a grower's facility, but rather to be an exact (albeit smaller) replica of the facility. A test room allows growers to try new products and strategies without worrying about affecting the rest of the grow. So, whether the tests fail or succeed, the facility's proven commercial crop methods won’t be affected.
Growers should think of their test room as a lab to test and isolate any new horticultural strategy, technology or product while keeping the other variables in the facility consistent. Whichever condition a grower considers changing and improving should be the only difference between what’s happening in the test room and what’s happening throughout the rest of the facility. A test room allows growers to benefit over the long-term by creating the freedom to test incremental changes and variables over time. This lets the grower implement new strategies when they work and discard strategies that don’t.
Growers should be sure to use the same metrics throughout the regular harvest cycles to measure variables such as growth, weight, and potency and then make an informed comparison by comparing it to the metrics of the test room.
When growers compare their facility results against the same test room metrics, they can zero in on subtle differences. Every harvest now provides data that will help determine the experiment's efficacy, as well as identifying new opportunities to improve the grow.
1. Shine a little light on the subject
The light technology for grow operations is constantly changing and improving and it seems like every new light manufacturer makes the same claim that their technology is “the closest thing to real sunlight.” Smart and savvy growers, however, know that throwing out a few numbers doesn’t make the claim true, and without real data, they probably won’t be eager to switch over to another manufacturer.
Even though cultivation experts aren't necessarily lighting experts, they definitely recognize lights are a major driving force in any operation. That’s why it’s important to take advantage of them as indicators of the operation’s energy consumption and operating costs. It’s in a grower's best interest to find a light that performs best for them in cultivation while also providing lower maintenance costs and high energy efficiency.
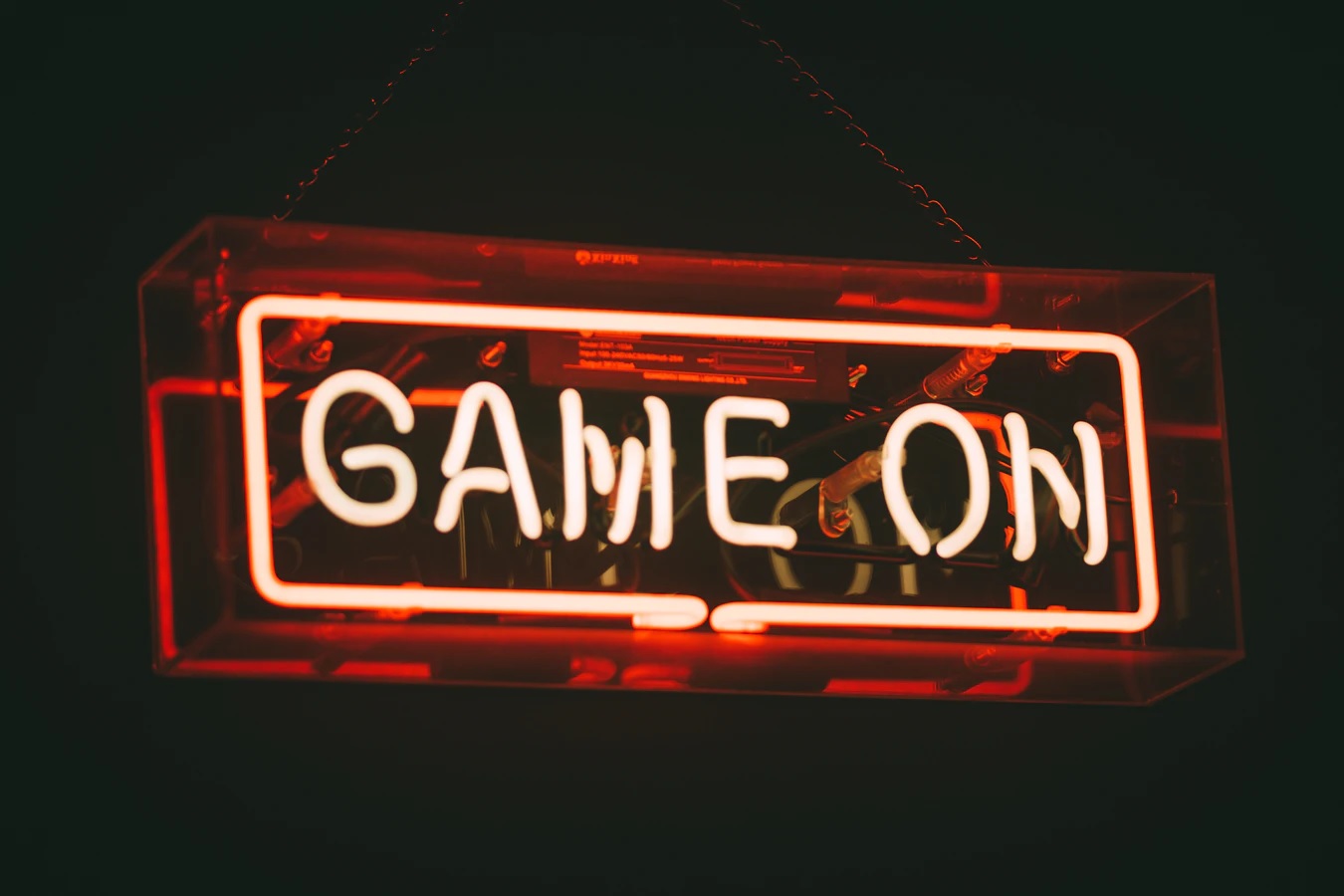
In a test room, growers can test a new light they're interested in and by performing their own research, see if it’s something they’d like to incorporate into the facility. In this particular experiment, the new light is the variable.
As mentioned previously, test rooms only need to be large enough for 10-20 plants. It’s important that these plants in the test room are the same cultivars growing in the rest of the facility. Again, test rooms needs to be set up as a smaller scale copy of the rest of the facility to make any meaningful comparisons, so feeding/watering schedules, media, and environmental conditions should be identical in both spaces. With everything else controlled, a grower can test the new light (being sure to follow the manufacturer’s directions and installation guidelines to maximize the results). There are some key specs growers will want to measure through the duration of the test to help them establish a baseline:
- the power consumption of the new light in kW;
- the average PAR (Photosynthetic Photon Flux) for the footprint of the light;
- its luminosity in PPFD (Photosynthetic Photon Flux Density). PPFD measures the amount of PAR that actually arrives at the plant canopy;
- and most importantly, the total weight of the flowers from each plant wet and dry, along with potency (THC and CBD) and overall perceived quality.
Lighting companies that only publish the PPFD at the center point of a coverage area are likely overstating the true light intensity of a fixture. A single measurement does not tell growers much, since, depending on the efficacy and quality of the fixture, many horticulture lights are generally brightest in the center. Light levels decrease as measurements are taken towards the edges of the coverage area (light footprint). To ensure growers get actual average PPFD values over a defined growing area, they must test the measurement distance from the light source from multiple points at canopy level to ensure accurate values.
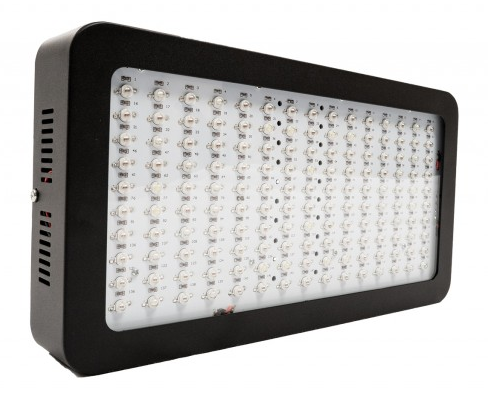
So, a test room is perfect for this application before the young plants are introduced!
Then, if the light performs as expected (exceeding the results from the present lights), a new test can be initiated during the next cycle to see how well it performs with another strain.
The variable in this case will be the strain itself. Certain light brands perform better with certain specific strains.
It’s important to note that a plant’s metabolism is impacted by a number of complementary variables (lighting, feeding, temperature, humidity, CO2 levels, ventilation, and other factors all influence plant behavior and harvest results). When a grower changes just one variable, they might not get the results they’re looking for without then adjusting the next variable, and the next, and so on. This would not be feasible in a production environment, but with a test room, growers aren’t limited by the need for a successful harvest—instead, the motivation is to continuously improve the specific “recipe.”
2. PUTTING DOWN ROOTS
Growing media directly affect the health and bounty of the plants in any given facility. As the old adage, “The Bigger Roots, The Bigger the Fruits” goes, a commercial grower owes it to their bottom-line profit margins to use test rooms to experiment with different forms of media. This is especially true for growers who prefer to grow in soil. Talk to any commercial grower whose media of choice is soil and they’ll report there’s practically an infinite number of paths to create the perfect soil mix recipe. Growers who cultivate in soil often consider their recipe to be as important as any other element in the environment. To test and perfect requires a test room. The recipes for the ingredients and especially the proportions (the key to any recipe!) of each ingredient is a jealously guarded secret for most commercial soil growers. So much so, that they remind journalists that they don’t feed their plants, they feed their soil! They develop and test their recipes in a test room where the recipe of ingredients added to the soil base becomes the variable.
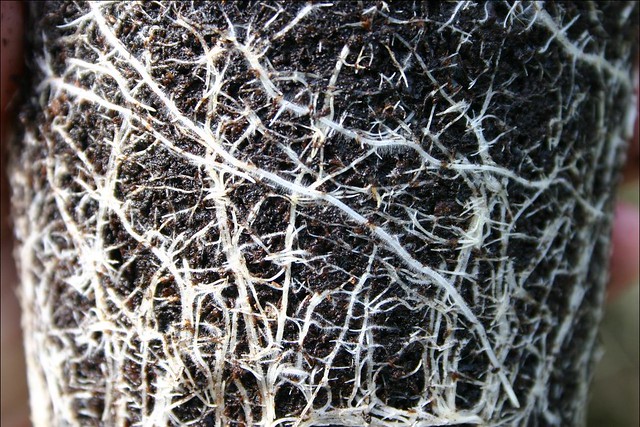
New hydroponics and aeroponics systems are perfect fodder for a facility’s test room as well. This is because for hydroponics, the media of either peat, coco coir, clay pellets or rock wool is often not the main variable being tested. It is the new hydroponics system itself that becomes the variable! For example, growers who strive to be on the cutting-edge of every new development in commercial cultivation improve their operations substantially, and just have plain old fun experimenting with a new hydroponics system in their test room every time one is introduced onto the market. It’s all fun and games before somebody figures out that from their own carefully calculated experiments using their test room, many “die-hard” soil growers have made the complete switch from soil to hydroponics when a particular hydroponic system employed in their test room has proven itself to be more efficient, economical, and impactful to the bottom line.
3. PLANT NUTRITION CAN BE FINE-TUNED IN A TEST ROOM FOR “FAT” BUDS
Especially suited for hydroponics growers, a test room is ideal for trying new hydroponic nutrient solutions. Although nutrient producers carefully define the exact ratio of nutrient in an irrigation tank, depending on the stage of growth, large commercial hydroponics growers need to be very careful when trying a new pre-mixed nutrient product since one reservoir can water and feed over a thousand plants in the main system. Even the slightest error in nutrient dosing can result in catastrophe, especially in hydroponic applications where there is no soil or soil-less media as a buffer.
Flowering stage can pose even greater challenges since many cannabis strains require a special mixture of nutrients that most nutrient companies don’t account for. In many cases, one size just doesn’t fit all. Some cultivars will consume more of a particular element than others, some will produce higher quality with slight tweaks to the recipe. The list is nearly endless. With a test room, hydroponics growers can experiment with nutrient solutions when sampling a different brand, using their existing preferred brand with a new strain, or mixing their own to come up with a proprietary and targeted recipe for a specific strain.
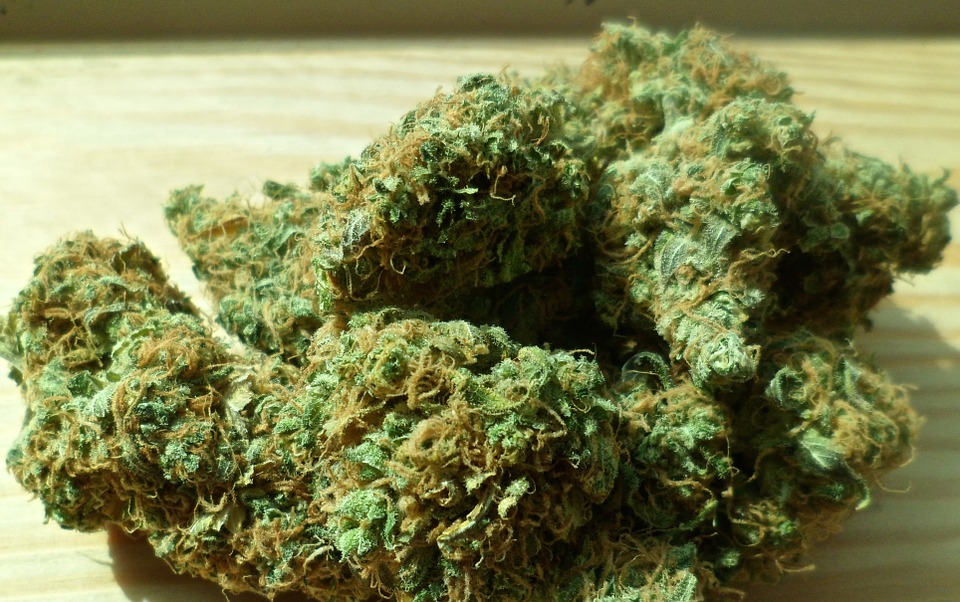
Testing of this nature isn’t feasible without a testing room. If production plants do not get enough (or get too much) of a given nutrient, quality and harvest volume will be negatively impacted, which will devalue an entire crop and hit growers right in the pocketbook.
A test room can offer a buffering zone with only a small number of plants where new nutrient mixes can be applied, and then fine-tuned until a perfect solution is reached and then synchronized with the flower development stages before it is fed into the main feeding system of the facility.
These are only three key areas, and growers know the variables and ideas that can be tested are nearly endless. Therefore, growers can use their test room to measure a wide variety of specific applications that promise improvement. KNOWING is far better than guessing, and with a test room, growers will know what to expect once they're ready to introduce new discoveries into their production SOPs.
Growers Network would like to thank Brandy Keen and Surna for this in depth look at the benefits of using a test room in your facility. What about you readers? Are you using a test room in your facility? We'd love to hear about your experience. Join our forums and start a conversation! Just click one of the "Join Now" buttons on this page.
10 Best Gift Ideas for Cannabis Connoisseurs and Growing Aficionados (2022)
December 7, 2022Developing and Optimizing a Cannabis Cultivation System
December 14, 2021Dealing with Insomnia: How Can CBD Help?
December 10, 2020Your Guide to Sleep and CBD
December 7, 2020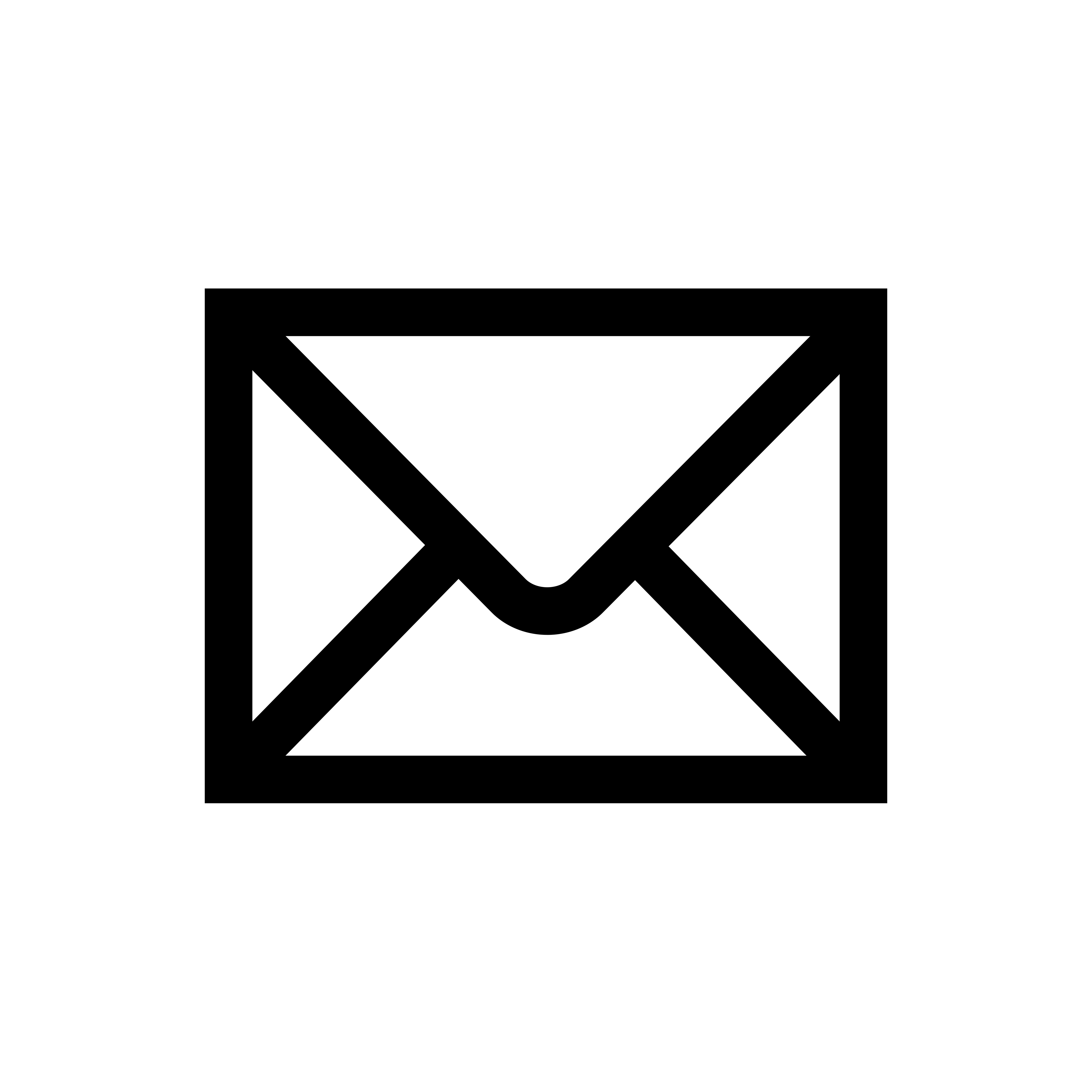
Do you want to receive the next Grower's Spotlight as soon as it's available? Sign up below!
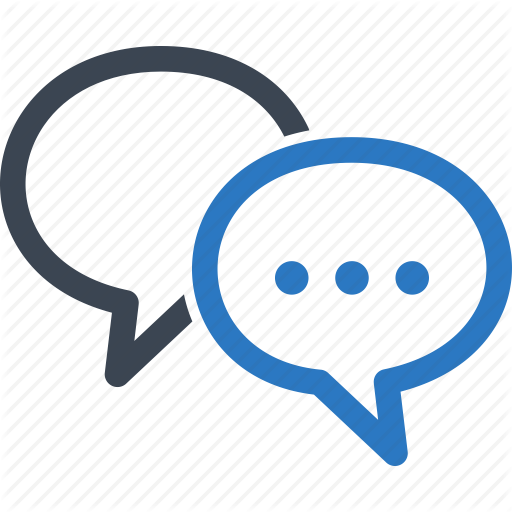
Do you have any questions or comments?
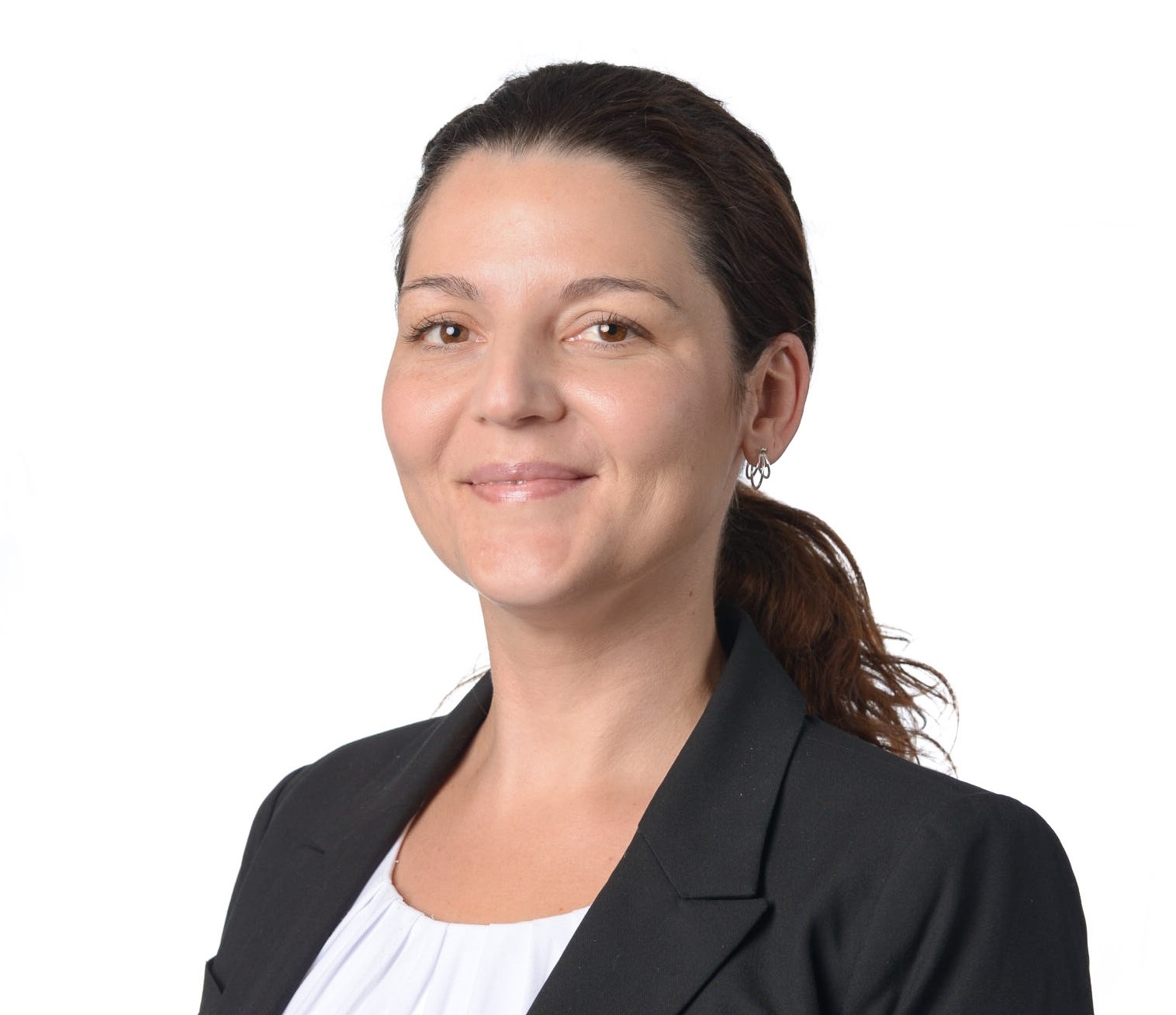
About the Author
Brandy Keen, Surna co-founder and senior technical advisor, has been designing and consulting for environmental systems in indoor agricultural facilities for over twelve years. She guides licensed PE's in facility mechanical designs, designs systems that meet local regulations and reduces energy consumption, and improve on standard practices.