Flip Sheridan of Cycloptics explains how the distribution of light from a luminaire is important in plant yield and size.
The following is an article produced by a contributing author. Growers Network does not endorse nor evaluate the claims of our contributors, nor do they influence our editorial process. We thank our contributors for their time and effort so we can continue our exclusive Growers Spotlight service.
Introduction
Editor’s Note: This article uses a lot of technical terms! Be ye forewarned.
Regardless of the type of lighting system you choose (CMH, HPS, MH or CMH/HPS hybrid, LED), it is important to understand before purchase and installation how well the reflectors and luminaires will deliver a uniform PPFD (photosynthetic photon flux density) measured as µmol/m2/sec over the plant canopy as it changes over time. The uniformity of the target minimum PPFD intensity over the full plant canopy is critical to optimizing the dry weight yield per plant, which translates into increased profits per harvest.
Think of it this way. If each of the lamps you are evaluating produce the same PAR (micromoles/second) output, then the average PPFD light uniformity over the full canopy throughout the veg or flower cycles will be determined by the interaction the beam patterns from all the reflectors in the room. This is especially true for hybrid systems where the uniform homogenization of the CMH spectrum with the dominant HPS is key to optimizing the yield per plant1.
The efficiency of any prescribed nutrient regiment is also directly affected by light uniformity. Over the course of a year, plants receiving low light compared to the targeted PPFD average will consume more nutrients and that will unnecessarily impact profits.
Beam Patterns of HID Lights
Reflectors use horizontal or vertically mounted lamps. The beam pattern of a typical 1000W DE HPS, 630W DE CMH, or 945W DE CMH lamp reflector is rectangular, designed to provide approximately 4x6 foot coverage at 3 feet. These systems depend on overlapping beams from adjacent reflectors to fill in around the edges of the hot-spot directly below each light. Hot spots are the result of light emitted by the lamps arc tube exiting directly downwards without interacting with the reflector. Hot spots create uneven plant growth that negatively impacts dry weight yields and increased nutrient demand from the under lit plants.
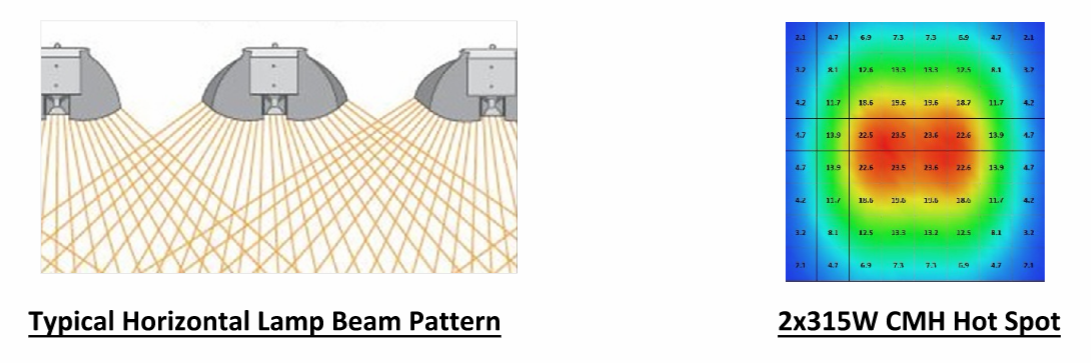
The beam pattern of Cycloptics vertically mounted 315W CMH reflector is the exception. The 3D compound curve geometry of the Greenbeams® patented reflector is the reason. Its 360-degree radial, high beam pattern was specifically designed to reflect off the walls of walk-in plant research growth chambers to create highly uniform, average PPFD intensity. It also means the plants receive light from an infinite number of beam angles that improves intra-canopy light penetration and uniform plant growth. This theory was studied and found to be true at Cornell University.2
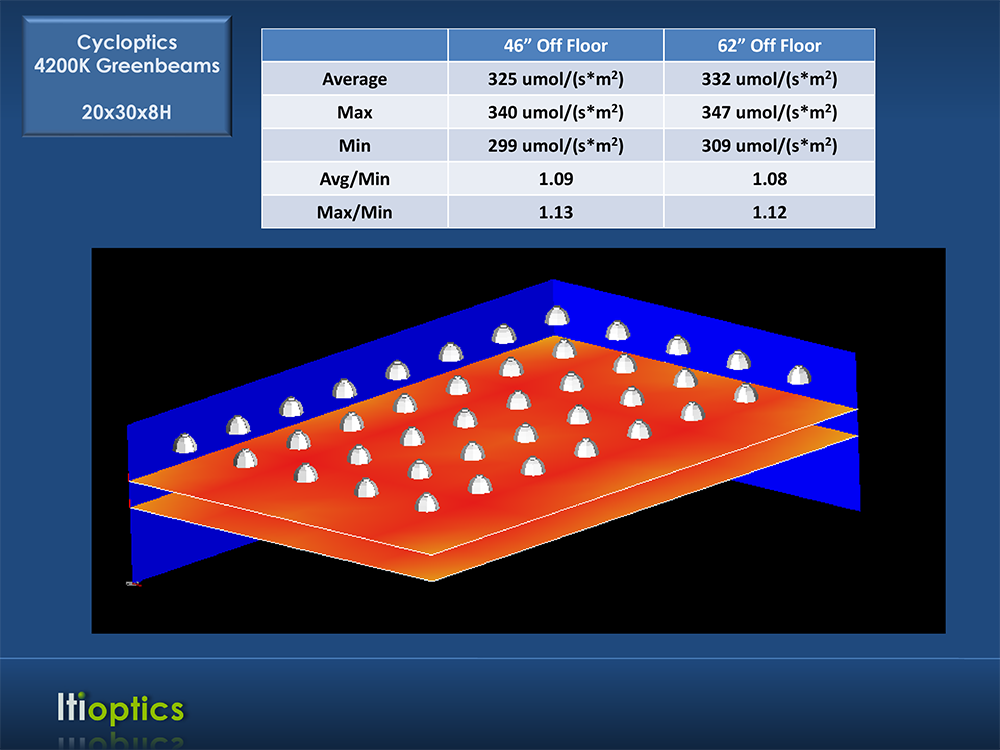
The ultimate result of this design is the ability to deliver 3D Full Volume Uniformity from the starting canopy height to the harvest height as shown in the model above for a 20x30 grow room. The average intensity and wall to wall uniformity over the full area of the room is virtually unchanged from a 46” off the floor starting canopy height to the ending 62” height. Plants are not static objects, and the canopy will move as they grow.
![]() |
![]() |
![]() |
![]() |
![]() |
![]() |
Lighting Height and Room Reflectivity
The grow room ceiling height relative to the ending harvest height of the cannabis strains in the room are other factors that should be considered during the design phase. Diffuse and specular surfaces are the two types of wall covering materials that can be used or applied to grow room walls. The differences between the two types of surface determine how the light that lands on them is reflected.
Light that lands on diffuse surfaces, like white paint or power-coated aluminum, reflects in every direction, including the ceiling. The reflectivity of high-quality flat, white paint is approximately 90% reflectivity with a drop off in the 600-700nm (red) range. By comparison, diffuse white ORCA® grow film is 94% reflective over the full spectrum.
Light landing on a specular surface is reflected at an angle opposite to the angle of incidence. This means the light will reflect downward onto the canopy in the case of indoor plant production lighting. Overall, this reduces light wasted on the ceiling from diffuse white walls. Examples of specular surfaces are polished aluminum or stainless-steel metal that are typically 85% reflective, and RadiantGuard® film at 95% reflectance. When designing a room with suspended lights you may want to consider applying RadiantGuard® to the walls as an inexpensive and easy way to improve energy efficiency.
In summary, to optimize dry weight yields it is critical that the lighting system you select delivers the best uniformity of average PPFD intensity over the full plant canopy for all growth phases.
Sources
- Comparison of Luminaires: Efficacies and System Design. L.D. Albright, A.J. Both, Cornell University, and Retrofitting Growth Chambers to Improve PPF Intensity, Efficiency and Uniformity. B. Bugbee, Utah State Crop Physiology Laboratory.
- Next-Generation, Energy-Efficient Uniform Supplemental Lighting for Closed-System Plant Production. D.S. de Villiers et al, Cornell University.
10 Best Gift Ideas for Cannabis Connoisseurs and Growing Aficionados (2022)
December 7, 2022Developing and Optimizing a Cannabis Cultivation System
December 14, 2021Dealing with Insomnia: How Can CBD Help?
December 10, 2020Your Guide to Sleep and CBD
December 7, 2020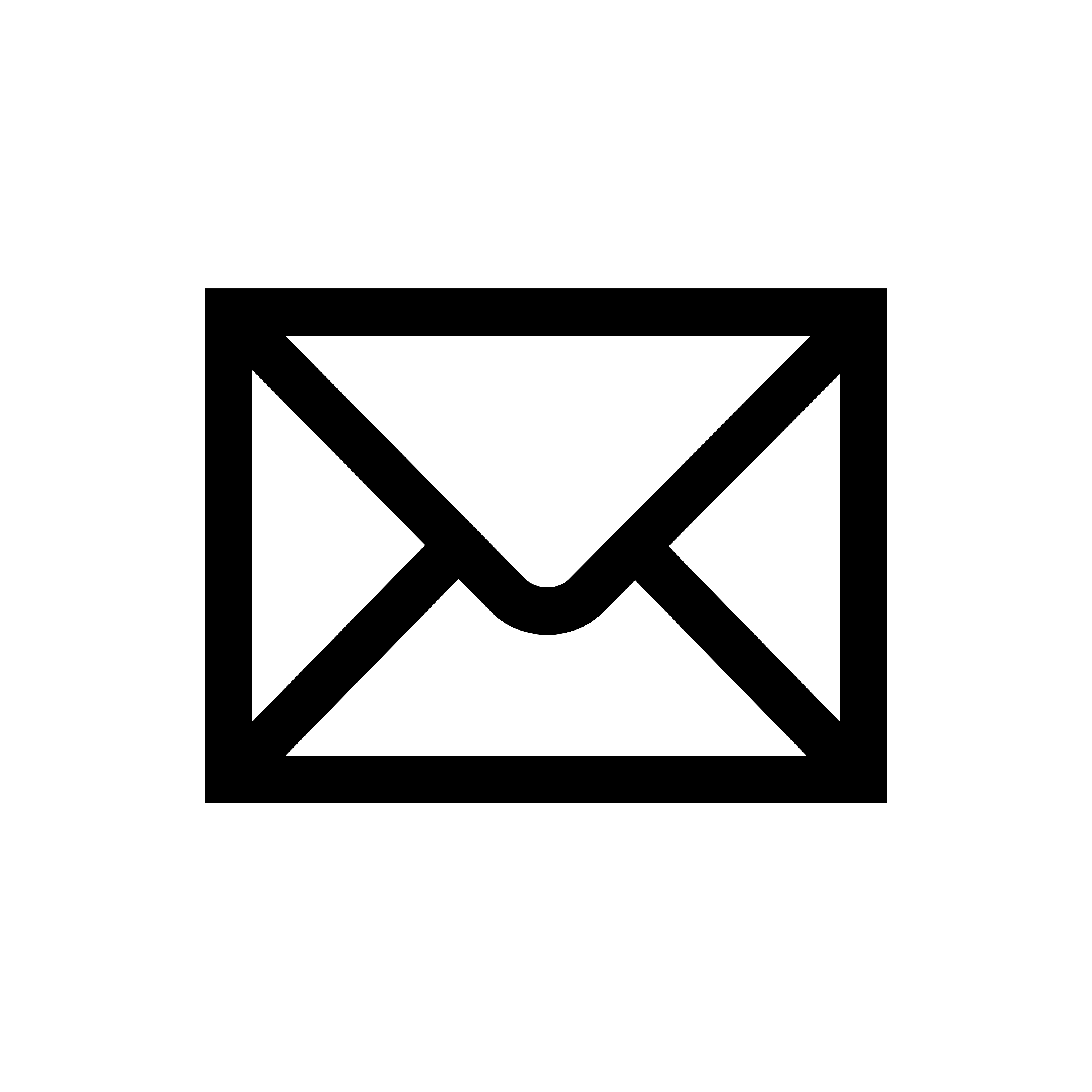
Do you want to receive the next Grower's Spotlight as soon as it's available? Sign up below!
Resources:
Want to get in touch with Flip or Cycloptics? They can be reached via the following methods:
- Website: http://cycloptics.com/
- Phone: 937.723.9818
- Email: webinfo@cycloptics.com
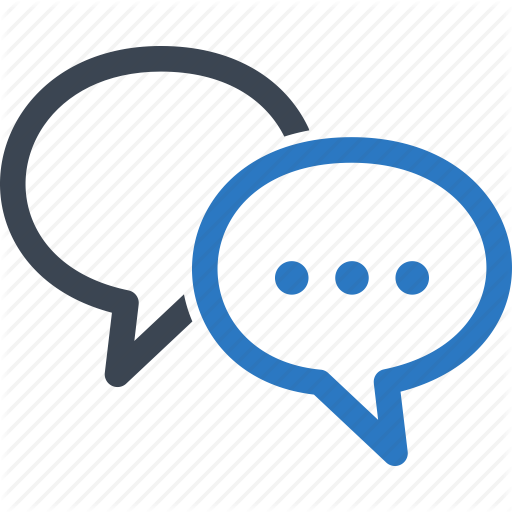
Do you have any questions or comments?
About the Author
Flip Sheridan is CEO of Cycloptics and an active member of NCERA-101 and AERGC. The optics of the patented Greenbeams 315W CMH reflector were designed in 2010 using proprietary software and with assistance from Cornell University as part of a USDA grant.