On the third episode of Canna Cribs, we take a jaunt over to Snowflake, Arizona to meet with Fife Symington IV and talk about what’s going on at Copperstate Farms and the inspiration behind this massive greenhouse grow.
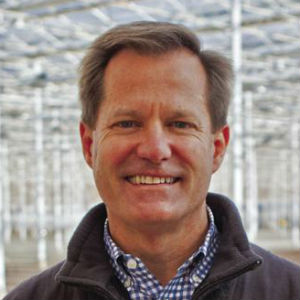
The following is an interview with industry experts. Growers Network does not endorse nor evaluate the claims of our interviewees, nor do they influence our editorial process. We thank our interviewees for their time and effort so we can continue our exclusive Growers Spotlight service.
To skip to any section within this article, click the links below:
Episode 3
Introduction
Nate (Narration): Hi, my name is Nate, owner of Growers House, one of the top suppliers of cultivation equipment in the world. I help growers source equipment and put together some of the largest, most advanced cannabis growing operations. I am constantly looking for the top products and methods needed to grow the best cannabis. Join me on a tour where I get inside access to the industry’s leading cannabis grow ops. This, my friends, is Canna Cribs.
Title Screen
Nate: It’s Sunday night, we’ve just rolled into Snowflake, AZ, and I’m about to go into a 40 acre greenhouse farm. And this farm used to be tomatoes, and now they’ve converted it completely to cannabis. They gave me a pass at security, and I’m about to go inside and meet with Fife, the owner, so he can show me how they run such a large operation. Let’s go inside.
Brief Interview with Fife
Nate: I just walked into Copperstate Farms, and I’m here with Fife, the owner of the facility. So Fife, I know you that you didn't start in cannabis, as none of us did. So what was your life like up until now? Fife: For the last 20 years I’ve been growing tomatoes, seedless cucumbers, and yellow and orange bell peppers in greenhouses. Basically, there was this green revolution going on right here in my home state. And I thought “Wow, I’ve been learning about commercial agriculture and greenhouse farming my whole life.” And now there’s real demand for it in the state of Arizona. Nate: Why don’t you give us the story on this facility in particular, because I know it’s rich? Fife: It’s got a great history, and the beginning of it might be a little bit apocryphal, but supposedly the first owner won the Canadian lottery and decided that he wanted to build a greenhouse in the best place he could find in North America. Looked all over the place, and built the south 20 acres. He was attracted to Snowflake because of the elevation, the light intensity, the number of sunny days, the quality of the water. He ran that operation for about six years, and then sold it to Eurofresh. They then doubled the size. Eurofresh ran it very successfully for a long period of time, and then they sort of got bitten by the global financial crisis. They went through an extended two rounds of bankruptcy. Then Naturesweet, which is a large producer of cherry tomatoes, bought this Snowflake facility and a facility in Wilcox, Arizona, out of bankruptcy. In my own time schedule, I think it was 2015. I thought “You know what, I really do want to get into the greenhouse growing of cannabis.” Right around that same time, Naturesweet announced that they were pulling out of the Snowflake facility. Fife: To me it was like a sign. The stars had aligned. I was looking around the state for where I was going to build a greenhouse, and here was 40 acres already built. We bought the property in September of ‘16, and we had our first harvest in August of ‘17. Nate: Wow. That’s great. And to think that so many jobs… Naturesweet probably pulled out because they couldn’t be competitive with south of the border crops from Mexico, right? Fife: Yes, yes. Nate: And that’s happening more and more, and that means there are certain jobs in the US that are disappearing, and who’s going to pick up the slack? Fife: And it’s a perfect window for the cannabis industry. Nate: Fife, thank you so much for teaching us all about your facility. I know I have an early morning tomorrow with Jacob, one of your growers, and I’m really excited to see the rest of this facility. Fife: You’re in great hands with Jacob, so, enjoy your tour. Nate: Thank you so much Fife. Fife: Absolutely, thank you Nate.
Bridge
Nate: So we’re here in the breezeway, about to enter the mega facility greenhouse of Copperstate farms. And I’m here with Jacob, one of the growers here, and he’s going to give us an inside look at their facility. Jacob: Awesome, we’re happy to have you guys. Let’s go take a look around. Nate: Let’s do it.
Genetics
Nate: Wow. First room of the day. Jacob, where are we right now? Jacob: So this is the mother room right now. We’ve got all of our moms here. It’s basically the start of our process. All the cuttings are going to come from these plants. Nate: These mothers are really big. I’d like to get a closer look at them. Jacob: Sounds good, let’s go. Jacob: So, our mother room is 55,000 sq. ft. Got it broken down in 3 zones, so we’re standing in the B section right now which is our active moms. We’ll be taking cuts off all of these active growing points to be stuck in the propagation room later on. We’ve got about 150 strains represented across about 1200 plants. 100 strains are active, which we’re currently growing for production. 50, we’re growing for trials for seeds or phenotypes, trying to make sure we’ve got some stable genetics.
Propagation
Nate: Look at all these plants. This row must go down… I dunno, a hundred feet? Jacob: Yeah, so. On average we get 350 cuts per strain when we’re going on active cuts. 25 cuts per tray, and on here we’ll have a couple thousands cuts, so I think it’s around 3500 or so. Nate: Ok, so, you guys are using, it looks like… Grodan as a media? Jacob: Yep. We’ve got Grodan Rockwool cubes here, and their trays as well. We’ll go ahead and be using those for our production cuts. Grodan’s been amazing ever since we switched over to them, and I can’t see us switching over again unless we experience problems. Nate: And I noticed there’s almost this sawdust looking stuff on them. What is that? Jacob: That’s actually our BioBest program from Coprate (?). They’re beneficial insects like Swirskii mites and aphipar (?) to really cut down on the amount of bug pressures we see in this room, because really similar to the genetics mother room that we just left, there’s always plants in here. So we’re really restricted on the type of bio regimen we can use. They’re predatory on the pests and they don’t really do anything to the plants. They just live there and call it their home. They’ll leave as soon as the bug pressure that they were eating has left too. It’s kind of like they finished the meal and left the restaurant. Nate: Well, what about the difference between growing tomatoes versus growing cannabis? Jacob: It’s much much more massive. If you think about it, they had 250,000 tomato plants per 10 acres here, and those plants would last for months and months and months. We have a smaller number of plants, and they last for a smaller amount of time, so they’re cycling through much more rapidly.
Vegetation
Nate: Wow. Very impressive room. So this is much larger than the mother room we were in. So can you give me a sense of scale? Jacob: So this is actually about twice the size of our mother room. We’ve got 2.5 acres of veg space here. It’s about 100,000 square feet. Nate: One room. 100,000 square feet? Jacob: Yeah, just one room. Nate: Looks like you’re growing in Coco Coir. I see Medicoir on the bags. What do you guys have going on for media and fertigation? Jacob: We start out with our Rockwool cubes, and then we immediately drop them into these Medicoir bags that you’re seeing. Coco is our desired media that we like running right now. After our trials back in August/October time, we saw that coco was the most profitable, and that’s what we’re looking into right now. Nate: And then for fertigation, it looks like you’ve got a lot of drip line here. Jacob: So we have all Netafim drip systems. We love the real pressure regulating aspects of a lot of their products we’re using right now. It really makes sure that we have a uniform fertilizer and irrigation distribution between all the plants we have spread out across the zone. Nate: So whether it’s in this corner of the greenhouse or that one, they’re getting the same amount of water every time? Jacob: Yep. Nate: So what about nutrient regimen? You guys using anything else other than your own custom blend? Jacob: So we do use one product or a few products through a company called Key to Life. They do some amazing nutrient work. We’re currently using their Silver Bullet sulfur for foliar applications. We also did some experiments with their molasses as well. It’s just a great nutrient company out of Colorado. They’re doing a bunch of great stuff as far as cannabis fertilization. Everything that we do is based on plant reaction. It’s not just a matter of every plant needs this. We try to make everything as uniform as possible, but at the end of the day, they still tell us what they want. Nate: I really want to dig into these LEDs that you have. Can we take a closer look at these? Jacob: Yeah, let’s go hop on one of those scissor lifts and take a closer look.
Bridge 2
Jacob: So these are the new LumiGrow Pro 650e’s with a SmartPAR module. I can run the entire lighting system remotely from my phone. It’s an extremely user-friendly system. Like you said as well, I’ve got complete control over this. So increasing the amount of blue spectrum or blue wavelengths in the last couple days of flower actually improves terpene retention. So you can improve your potency based on your lighting strategy even in the last couple days of flower. Nate: These lights, they know if there’s a cloudy day and a few cloudy days. They have predictive analysis that might frontload the amount of light that they get in the morning to make sure the plants are going to get enough light. Jacob: Exactly, so what it’s doing is constantly live-time measuring and analyzing the light conditions of this room, looking at our settings and our targets, and saying “Ok, how do I need to affect or change the instantaneous intensity of this light to make sure that we achieve this goal in the set timeframe?” Nate: As far as I know, this is the only fully automated LED solution that takes into account environmental factors, at least as far as I know. Jacob: Exactly, this is the only fully automated lighting greenhouse solution out there.
Flowering
Jacob: So we’re in house 44 right now. We’ve got about 7200 plants in here spread out across an acre and a half. That many plants, you’re going to get some really crazy smells first thing in the morning. Nate: Maybe… we can take a stroll down one of these rows? Jacob: Yeah, let’s grab a lab coat to keep us off the plants and we’ll go check it out. Nate: Jacob, one of the things I really wanted to get into coming into this flowering greenhouse is how you manage environmental controls. In Snowflake, Arizona, where in the summer it can be 100 degrees, and winter it can be snowing, and you have to grow a crop year round. Jacob: We have a Priva environmental control system and it’s just amazing. It takes into account all these different factors: Temperature, relative humidity, vapor pressure deficit… all of these crazy factors that we can use and create our own program and our own strategy. Nate: And the Priva system… that’s commercial ag software that’s used in tomato production, you guys were able to transfer right over to cannabis right? Jacob: Right, Priva was designed for large scale agriculture and it fits our needs really well here because everything is interfaced into once source, so I can control all of the environmental factors, all of our irrigation, lights, fans vents, whatever it may be, just from one platform. Nate: So you mentioned pruning just a second ago. I know you guys are using our Common Culture Trojan scissors. You guys buy a ton of them. But I want to go over… what’s your philosophy behind it? What are you trying to go for? Jacob: So the philosophy is just to pull off some of those lower shoots, auxiliaries, and little flower sites that aren’t going to produce much for us in the very end. So we pull those off and try to have the plant focus its growing energy on those four main heads that we created in the veg room. Nate: And this is the Grower’s Edge trellis netting. I know that you guys use this in a vertical fashion more than a horizontal fashion that I see so often. Jacob: So what we’re trying to do with this is open up the plant a little bit more, getting the airflow going down through the center of the plant. Right now we’re in monsoon season, so we went from 5-10% average humidity to over 50% within a week’s span. With that big of a change, you’re watching powdery mildew and other mold spores popping up. It’s something that we have to stay on top of with our IPM regimen, our environmental control strategy, and everything down to this trellising and pruning, making sure we’re helping the plants by keeping these pressures as low as possible. Nate: Jacob, I noticed you have these packets hanging up above your plants in the flowering rooms. What are those? Jacob: Those are part of our ProKure protection program. The ones you’re seeing right now are the ProKure D slow-release packets. They give us the ongoing ClO2 protection during the plant’s life cycle. We also have fast-gas ProKure G and V packets that we use in between harvest to clean the room of any remaining mold and mildew spores that could be airborne or in some really hard to reach places. It’s really essential for our IPM program to keep these houses as clean as possible.
Drying
Nate: Ok Jacob, I am not lying when I am saying this is the most beautiful drying room I’ve ever been in. I would eat off this floor, it is so clean. There is not one speck of dust. Jacob: We’re a medical facility, you’ve got to keep this to the highest level of cleanliness. Nate: Of course, and you guys have something I’ve never seen before. You have a wall pushing out air slowly. Jacob: So it’s a slow dry and directional air flow. We’ve got our south walls that’ll push air and our north walls that’ll pull air, and effectively it creates this real slow draft over the plants to make sure that we’ve always got new, dry air coming in, but we’re not blowing trichomes off the plants. We want to make sure we keep those crystals nice and intact. This was just cut down today, so it’s still really fresh. Can probably still get a real big whiff of vegetative and a whole bunch of terpenes. It’ll be here for about a week or so until we get to the right moisture content, and then we’ll go ahead and move it onto the curing room.
Curing
Nate: Jacob, this room is the curing room, right? I mean, it’s really cold and kinda windy in here. Loud too. Jacob: This actually used to be the original cooler back when this was a tomato farm. So this is where they’d store the tomatoes before they got shipped out on trucks to grocery stores all over the US. So, you’re actually hearing the AC from that old system, which keeps it nice and cool for our workers in here. When we originally started we were in these black totes that didn’t quite give us the airtight seal. We switched to CVaults because we realized the benefit in having a sealed environment cure in the little CVaults. Nate: So no light, no air. Jacob: Exactly. Also in these, we’ve got the Boveda moisture packs to help regulate humidity in the CVault, keep it at exactly 62%. Nate: Ok, for the Bovedas. I know some people use the 55%, some use the 62%. You like the 62? Jacob: We like the 62. It keeps a lot of those terpenes in there, we feel. It’s extra sticky, which a lot of customers like. Nate: Ok, so how much weed is actually in this store room right now? Jacob: Because this is also our storage room as well, we’re probably looking at over a ton. Close to 2 tons, 4,000 pounds of weed. Dried, cured, packaged, and ready to go. Nate: Wow, the market is hungry. Jacob: We’re ready to feed it.
Trimming
Nate: So I made my way into the trimming room of Copperstate Farms and I met up with Holly, who’s going to go over a little bit of what they do here. So Holly, what is your role here at Copperstate Farms? Holly: I am in charge of preliminary QA. What I do is when it comes out of the dry rooms, I take at least an ounce of it, trim it up myself, grind it up, and look at some under the microscope. That way I can document if there are any issues like seeds, pests, or mold, and catch that. Then I do the good things like how much it weighed, the density, is it larger than the last batch around, things we can compare to improve in the future. Nate: So that’s interesting. You’re almost acting like the end user to grade the cannabis in different… steps? Holly: Exactly, yes. Normally every strain runs through the GreenBroz first, and then we can send it to them because it cuts out about 70-80% of our trimming. Nate: Cool, I’m going to check out packaging. Holly, thank you for showing me around. Holly: Any time. Glad you could make it.
Packaging
Nate: So I’ve stumbled my way into the packaging department, and I’ve met up here with Ivan. Tell us a little bit about it. You’re running this department and maybe among others you were saying? Ivan: I’m the processing manager for everything that comes in from harvesting. As soon as harvesting comes in, I’m in charge of all operations. Right now we’re ramping up to 500 pounds. We’re anywhere from 200-300 pounds a week. Trim alone, we’re packaging up to 300-400 pounds per day. Popcorn, we can do anything from 100 to 200 pounds a day. We used Boveda packs to balance out our moisture. If the moisture comes anywhere from 10-11%, we throw in Boveda packs into the package. They work both ways. If there’s too much moisture, it’ll remove moisture, and if it’s too dry, they’ll add moisture. They work really well for us.
Extraction
Nate: So we made our way out of packaging and I found myself in this very quiet, sterile room with Alec. Alec, what’s your role at Copperstate? Alec: I’m the extract lab manager here at Copperstate Farms in Snowflake, Arizona. This room right here is very clean and it is the material prep room. We take all flower from the processing area or this big freezer behind you and grind it, mill it, and get it prepared for CO2 extraction. Nate: This Vitalis (?), is that the next step in the process? Alec: That is essentially the next extraction step. Nate: Why don’t we jump out of this room and go show everyone that piece of machinery? Alec: Sounds like a plan.
Bridge 3
Alec: So this is ELSA, the Vitalis Q90. It’s able to process about 75 pounds of biomass per day. Currently we’re running 25 pounds of material, we expect to get around 2000g of crude oil from it. Nate: Alec, I saw this in the corner and it looks like a really insane crockpot, but I know it’s much more than that. Can we go into this guy? Alec: Yeah, so this is our Delta Separations CUP15 Ethanol extractor. C1d2 approved, able to process about 30 pounds of flower every 35 minutes. Beauty of this system, in an 8 hour shift we can process about 300 pounds with a single technician. Nate: And how much does a machine like this run? Alec: It’s actually a pretty reasonable pricetag. It’s only about $84,000 give or take depending on what additions you get. Nate: Wow, that’s crazy. And this is making a lot of the things you see in vape pens, distillates, shatters… Alec: With this we can make isolates, sauces, shatters, crumbles, we can whip different products. Like you were saying, we can make distillate, distillate cartridges. This is really kind of an all-in-one system. Set it, forget it. It spins, it dices, it sets the prices.
Bridge 4
Nate: I’m here with Bodhi, one of the cofounders of Root Sciences, this really awesome piece of equipment behind me. And he’s going to go into it a little bit so we can learn a little bit more. So Bodhi, what is this? Bodhi: So, basically what we’re doing is putting the feed stock into the feed tank. This is already prepped oil ready to go. We use gear pumps instead of a gravity fed system which allows us to pump oil through the machine instead of using gravity which gives you a less precise separation of the cannabinoids. So on the first pass, we’ll want to pull out the terpenes. On the second pass, we’ll target cannabinoids. We do that through temperature and via vacuum. We’ll modify those parameters to target terpenes or cannabinoids. The check valve is our barrier to vacuum. From there it goes into the degassing arm. The degassing arm helps us to alleviate entrainment issues, which means we don’t want any off-gassing happening on the evaporator, which can cause splashing for residue to condense on the coil and it’ll come out in your distillate. So the oil comes down the evaporator wall. The rotor is creating a thin film which agitates the oil and provides maximum surface area. On the first pass, the terpenes are vaporizing off of the wall, recondensing on the coil, coming down, and coming out this side. The rest of the oil is staying on the evaporator wall and coming out this side and pumped out here. Once all the oil has run through the feed tank, we’ll take this oil, which doesn’t have any terpenes in it any more, put it back into the feed tank, change the parameters, temperature, vacuum. We’ll pull a deeper vacuum, run it a little hotter. And then we’re going to do the same process. But because of those parameters, now the cannabinoids are going to vaporize off the wall, recondense on the coil, now you’re going to have distillate coming out this side. Your residue, which is basically trash, is going to come out this side. Root Sciences has been doing distillation for 7 years, so we have the expertise and the know how to run these machines, train people on these machines, support these machines, which you’re not going to see from other competitors. The other competitors that are out there are manufacturers. They don’t know the process of extraction or winterization and filtering and solvent recovery. They know distillation. Root Sciences knows the whole gambit. We started out in concentrates and extraction. You’re not going to find a better piece of equipment in the market. Nate: Very precise piece of machinery right here.
Edibles
Nate: Welcome everyone to this week’s episode of cooking with cannabis. I’m your host, Nate Lipton, and I’m here with Good Things Coming, Sarah, and Alex. Why don’t you tell us how Good Things Coming came about? Sarah: So Good Things Coming is started by industry-leading chefs. We came together in Phoenix and we saw that there was a huge need for chef-driven edibles. We took our experience working in high-intensity kitchens. We took that discipline and applied it to a really badass brand of edibles. Nate: So Alex, tell us a little bit about your background. Where did you come from and how did you end up getting here? Alex: I’m original from Spain, Barcelona I mean. I started in some pastry schools in Barcelona, and then I started working for one of the best pastry chefs in the world. I just moved to Arizona last summer, and they told me about the brand and I said “Let’s do it.” Nate: I hate to use the phrase, but you must be like a kid in a candy store. In this 4000 square foot commercial kitchen with all the new… appliances? Tools? Equipment? I don’t think anything can help me close out this show better than your company’s name… there’s Good Things Coming to Arizona and maybe even the rest of the country. Sarah, Alex, thank you for having me.
Analytics
Nate: So I’m here in a very unique laboratory inside of Copperstate Farms. Now I’ve never seen this before, but this is a separate business operating on the same property of Copperstate Farms. Now this business is run by Catherine, and what is the name of your guys’ business? Catherine: Well, welcome to Bioanalytical Laboratories Nate. Nate: Why thank you. It’s a laboratory of course, I see all the equipment. But what do you guys do here? Give me the skinny. Catherine: We test for cannabinoid potency, we test terpene profiles, take a look at that, and we also take a look at any microbial activity that may be present since we are working with biological systems. Would you like to help me with my microbial assay? Nate: I do not know what that means, but it sounds like fun, thank you. Catherine: Great. Come on! ... Nate: I hope they fast motion this part. Catherine: We’re currently evaluating the Cure Advantage system. They’re a local company that’s located right here in Tucson, Arizona. The Cure Advantage staff monitors the gases that are released during curing. They do that in realtime. Nate: So it’s almost like you put the flower into a receptacle, and rather than burping it manually, that system will handle any exchange of gases within it so that you can cure faster. Catherine: Right. And it’s a very simple system to use, dried flower is put in the containers, and they’re connected with quick connects, and it’s that simple. It has the potential to reduce labor costs and elimiNate any contamination. Nate: Yeah, cool. I want to hear more about that Cure Advantage as you guys get farther along in your testing. Catherine: Ok. I will keep you updated. Nate: Thank you Catherine. So that wraps up my tour of Copperstate Farms, Catherine, thank you so much for showing me around this analytical lab. It’s the first one I’ve ever been to. Catherine: Well, I hope that you enjoyed yourself Nate, and thank you so much for honoring us with your presence. Nate: Thank you.
Final Transition
Nate: After a long day of hanging out at Copperstate Farms, I’m finally here with my crew. Jacob is joining us, and I got some of these. Would you like one? Jacob. To good times, to high times. Canna Cribs Episode 3: Copperstate Farms. That’s a wrap. I think we’re going to go hang out with our crew. Jacob, thank you for joining us. Let’s go.
Abbreviated Article
Editor's Note: Growers Network appreciates its readers! If you are limited on time, we are now offering abbreviated versions of our articles. Click below to view.
About Copperstate
How did Copperstate Farms start?
Copperstate is a MASSIVE farm. How did you secure the capital necessary to acquire and renovate the facility?
How difficult is the conversion process for facilities that were designed for tomatoes?
What distinguishes Copperstate? What’s its competitive advantage?
What happened while you were pitching Copperstate to the town of Snowflake?
Guiding Philosophy
Where do you picture the future of the Arizona cannabis market in 10 years?
What’s been your biggest challenge?
What’s been your biggest success?
What was your response to the 2016 ballot initiative in which recreational marijuana use in Arizona was not passed?
If you like the abbreviated article, let us know in the survey at the bottom of the article! We're always interested in hearing your feedback.
If you want to read more, you can read the full article below.
About Copperstate
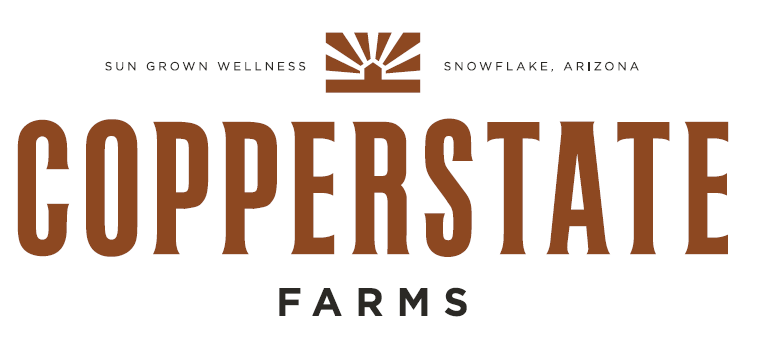
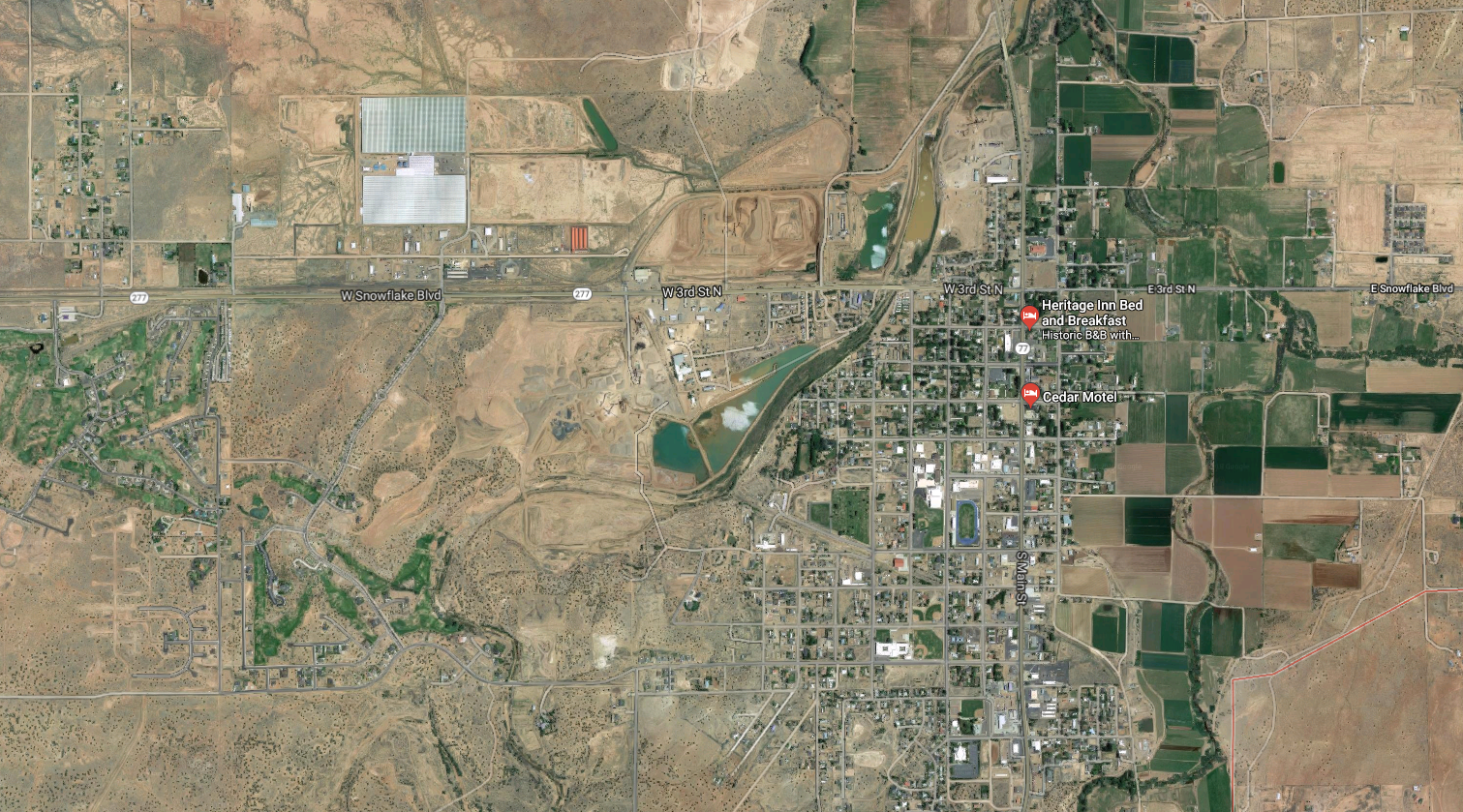
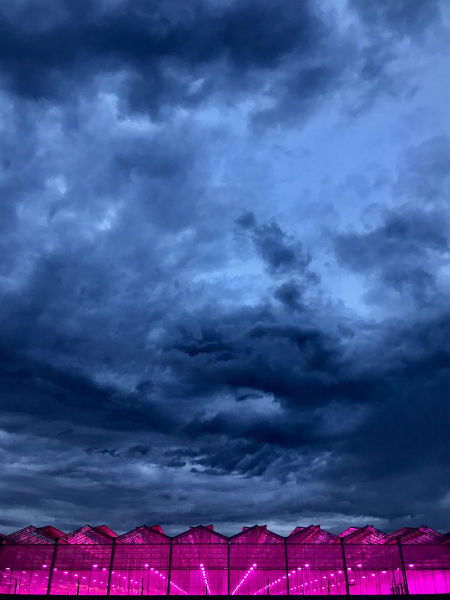
![]() |
![]() |
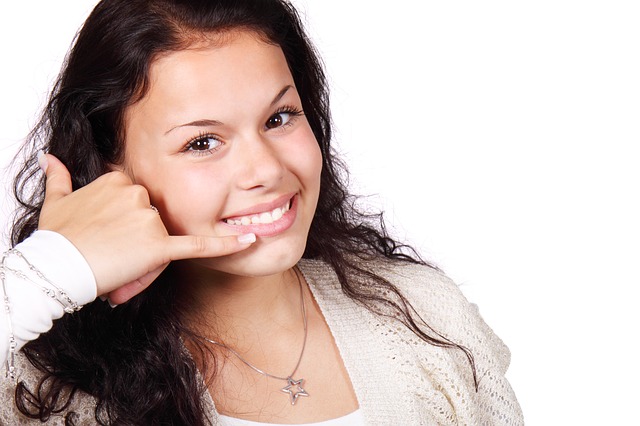
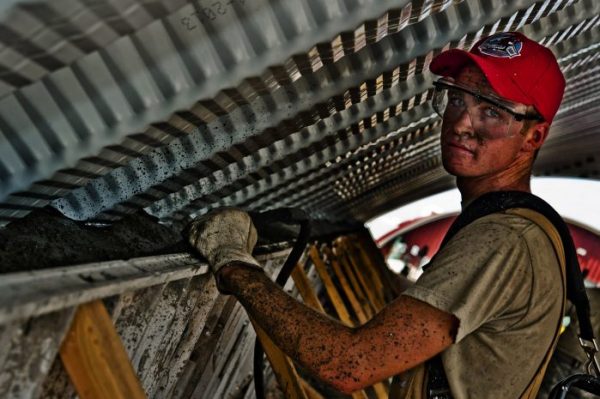
Guiding Philosophy
I predict that 10 years from now, we will have adult-use [cannabis] legalized in Arizona.Fife Symington IV
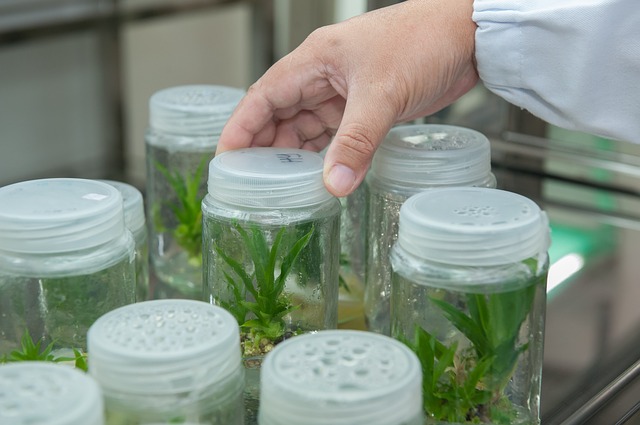
If an adult use bill is put before voters, do you think it will pass?
About Fife IV
Want to grow like Copperstate Farms in Canna Cribs Episode 3?
Follow the links for everything you need!
- Media:
- Nutrients:
- IPM:
- Irrigation:
- Trimming:
- Curing:
- Packaging:
- Processing:
- Extraction:
- Analytics:
10 Best Gift Ideas for Cannabis Connoisseurs and Growing Aficionados (2022)
December 7, 2022Developing and Optimizing a Cannabis Cultivation System
December 14, 2021Dealing with Insomnia: How Can CBD Help?
December 10, 2020Your Guide to Sleep and CBD
December 7, 2020
Do you want to receive the next Grower's Spotlight as soon as it's available? Sign up below!
Want to get in touch with Copperstate Farms?
You can reach them via the following methods:
- Website: https://copperstatefarms.com/
- Email: info@copperstatefarms.com

Do you have any questions or comments?

About the Author
Hunter Wilson is a community builder with Growers Network. He graduated from the University of Arizona in 2011 with a Masters in Teaching and in 2007 with a Bachelors in Biology.